A brand
synonymous with class and style has an ardent journey to describe.
like a simple pair of jeans has an amazing story to tell. A factory tour of Numero
Uno, the youth icon in fashion, has a fantastic tale to tell.Inspired by
the western music and Pop culture of the 80’s, the Indian youth believes in
being vocal about everything, and saying it out loud.
Narinder Singh, MD, Numero Uno Clothing Ltd. saw the gap of the ardent need of
the best and demand for denims for the masses, and so began to procure denim
fabric from the domestic market and convert it into a cool pair of jeans.
Uno was born.
fabric and production of denims were always there. However, his strong
determination and his love for denims, surpassed the obstacles and Mr. Narinder
Singh pursued his dreams with locally assembled machines to manual washing and
scraping and created designs and patterns.
and determination created huge demand in the market and the retailers and
industry veterans rated Numero as A1 quality product, and that’s how the brand
got its name, ‘Numero Uno’.
at its core, Numero Uno has diversified into a complete range of casual wear that can be complimented with a cool
pair of jeans. These include shirts, tees, jackets, belts, shoes, bags etc.
Numero Uno is probably one of the very few brands that designs, manufactures
and markets its denims. They have three manufacturing units, 2 in Gurgaon and
one in Dehradoon.
boasts of more than 180 exclusive brand
stores across more 100 cities, and is largely present in more than 700
multi-brand outlets and large format stores like Shopper’s Stop across the
country.
brand presence in North, Numero Uno has been steadily increasing it footprints
in rest of India. The brand shall reach Mumbai, Hyderabad, Belgaum & Nashik
too. Numero Uno has also achieved a pan India presence by tying up with leading
ecommerce players like Flipkart, Myntra, Jabong & Snapdeal. Online shoppers
can also indulge in shopping at www.numerounostore.com.
The brand Numero
Uno believes in accepting/adapting change as and when the time is right. They
believe in creating great value for the consumer and commit the highest levels
in terms of product quality, design and integrity. Keeping in mind their
consumer and his aspirations, Numero Uno took a new approach in 2012, and added
a new logo “NU” to its current NUMERO UNO jeans wear, a short-form of Numero
Uno and the logo is strategically used to represent, ‘New’. This reinstates the
brand’s commitment to innovation and ‘newness’ in its offerings.
FROM THE BRAND
2000, Numero Uno’s campaigns brought out the romance and love for all things
beautiful and nice. This phase saw Laxmi Menon, Marc Robinson, Anupama Verma,
Mini Mathur, Aditya Roy Kapur and Bruna Abdullah some of the leading film and
fashion personalities endorsing the brand.
face of the brand is Lisa Haydon, a personification of fashion, attitude,
confidence who flaunts her unique individuality with so much ease.
manufacturing process is divided into 3 parts – design, production and laundry which
any factory produced garment goes through. However, denim is a fabric that goes
through more processes and that’s why all denims have an individual appeal.
designers conceptualize the look of their denim collection one season in
advance. Each element plays a crucial role in enhancing the look of the denim.
concept pr an idea gets translated into a design or style. The sizes, fit,
& ratio are studied while making the prototypes. Design patters are
developed and cut on the basis of design sheets which involves a close
coordination between the designer and pattern makers. The layering and cutting
of fabrics is programmed through automated computer aided design systems.
is like hitting the bull’s eye. Numero Uno’s understanding of the Indian body
type, consumer preferences and extensive
fit trials have helped us reach a position where the brand is known for its
amazing fits. From skinny & slim fit
to straight fit and from mid-rise to low rise, the choices are plenty.
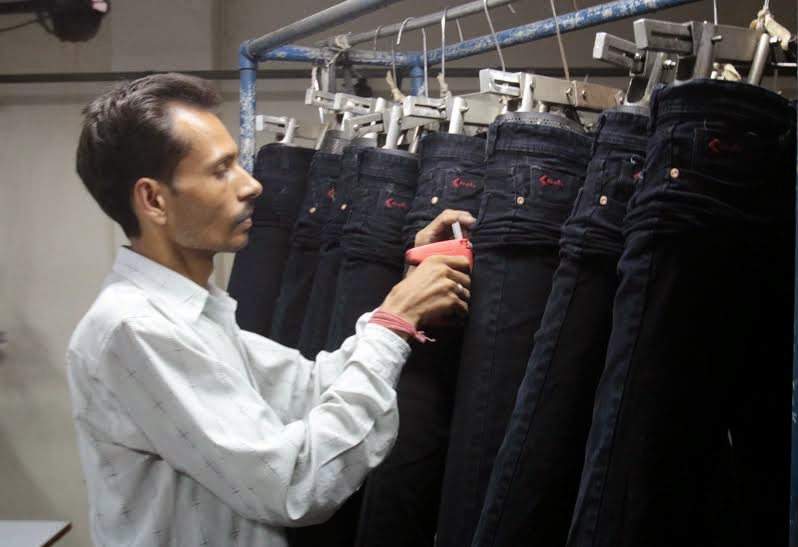
knowledge and latest machinery, the predefined CAD patterns help in cutting the
fabric basis style & fit and achieve maximum unison of patterns and designs
with minimum wastage. The size, fit & ratio is studied and tested while
making the prototypes.
interesting in this process is that 11 to 15 parts are stitched together to
make a pair of jeans. The things usually added to a bare pair are belt loops,
zipper, buttons, pockets, inside and outside, rivets & the leather patch. Stitching
is done with the help of high speed stitching machine. Machines used are chain stitch machine, Over
lock machine, Belting machine, Feed off arm machine, Loop making machine,
Bartack machine.
a denim is a denim until it is washed. All denims are made from same fabrics,
it’s the washes and post treatments that bring out the character of a denim. It
gets its final look at this stage when it goes through Laser patterns, hand
scrapping, Ozone bleaching, Stone washing etc. It is the key element that
differentiates one from another. Washing involves a lot of experimentation as
fabrics react differently to different washing agents such as pumice stones,
enzymes, silicon etc. Depending on the look that is to be achieved, following
washing processes are required:
Ozone Bleaching
Laser machine
Hand scrapping
Stone washing
G2 – Waterless washing
machines
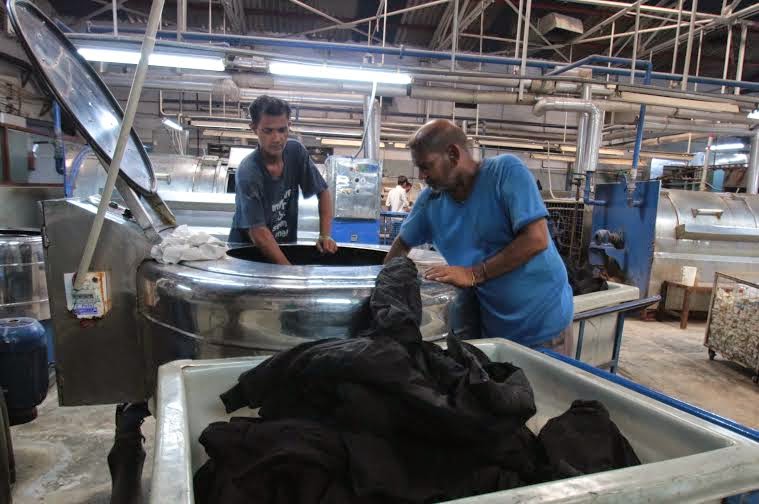
Laundry is a term generally used to describe a philosophy of textile care that
uses electricity and oxygen in a unique way to replace
many of the chemicals normally used in a traditional washing process.
electricity are used to create ozone. Ozone is dissolved into water and applied
to the wash wheel in place of the chemicals. It prevents the formation of Fungi
and prevents staining. 100 kg’s of back staining can be removed in 10 minutes.
begins with a paradigm shift in traditional laundry fundamentals.
Improve efficiency and reduces operating costs of a laundry. It
greatly reduces the environmental impact of traditional laundry operations.
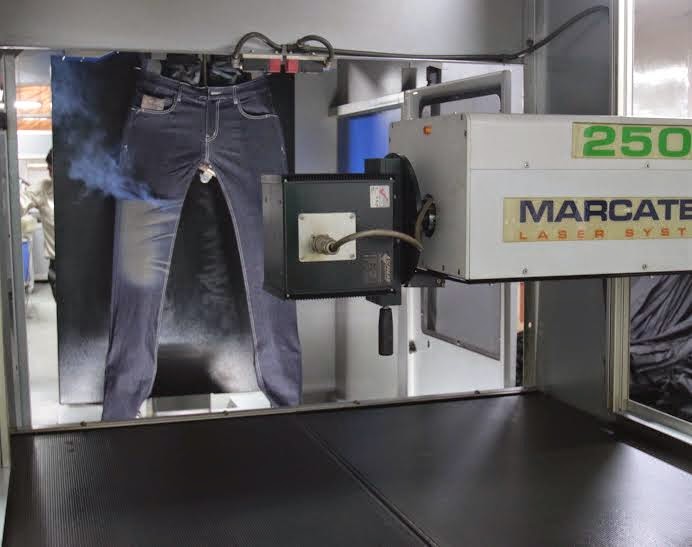
Machines are used to create whiskers or moustaches on the
denim, as per the predetermined pattern. This helps in eliminating the manual,
time consuming & hazardous process of sandblasting. Laser machines help
replicate the same effect on all garments consistently. Only the brittle denims are scrubbed with
sand paper in order to obtain whiskers.
Hand
scrapping process, the placement and pattern is marked on the
garment which is mounted on balloons filled with air and scrubbed with sand
paper on engraved pattern lines. This operation requires high skilled labour
who can handle uniformity and sequence in whisker line.
was perceived as the most
polluting stage with chemical discharge polluting the water and the dust, a
precursor to respiratory issues.
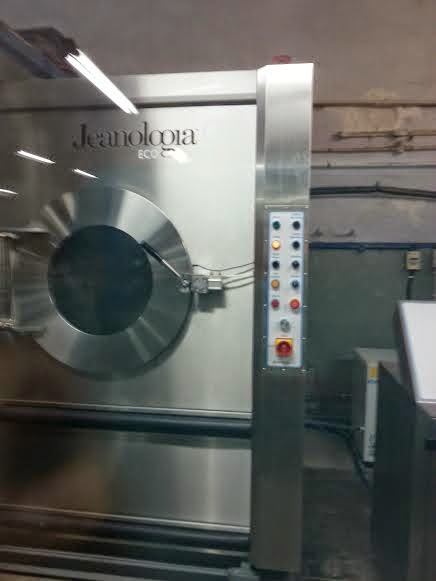
The laundry process has seen a paradigm shift,
thanks to Jeanologia, their research
& technology partner from Spain, one of the best in the world for washing
technologies. The latest processes implemented at Numero Uno is more efficient
& environment friendly.
washing machine uses 90% less water & 80% less electricity while
washing a garment.
washes are also done with the help of pumice stone to give a
faded and worn out appearance. This is usually accomplished either by washing
the jeans with pumice in a rotating drum.
Waterless Washing Machine that washes jeans with about 60 % less water and almost no chemicals…….!!
How & what is does : Air
from atmosphere is transformed into a blend of active oxygen and ozone called
‘Plasma’. This plasma is used to wash & the age garments. The plasma is
transformed into purified air before it is returned to the atmosphere.
Capacity: The
machine has a capacity of 50 kgs ie it
can wash about 3000 jeans in a day. G2Ts programmable software system
automatically adjusts gas concentrations to reflect load conditions (i.e.,
jeans, tees, wet, dry, etc).
environment: From
a case study of actual production in the US, it has been found that G2T can
result in 67% savings in energy and water, 55% savings in time and 85% saving
in chemicals and can thus provide a saving of $0.44 per garment washed besides
contributing to environmental protection and reducing health hazards for the
workers.
Benefits.
Removes back-staining & loose
indigo without detergents.
Bleaches without using chemicals.
Eliminates the need for Potassium
Permanganate spraying.
Improves Crocking in Dark finishes.
Creates unique yellow-cast for true
vintage looks.
hand in hand with its commitment for nature, greenery and green practices. Eco-friendly technology such as lasers, ozone & G2 have
been employed in order to prevent the use of chemicals, save water and protect
the environment. Several years ago, Numero Uno did away with the process of
sand blasting, which could effect the health of the workers.
and reducing its dependence on them. With these measures we use Solar energy
for water heaters (used in washing the garments),
lighting the 10 acre large campus that houses the plant, the head office
and a warehouses. These solar heaters
help save upto 10,000 litres of
diesel fuel per annum. Wind ventilators are used to push out
hot air from the factory floors instead of the industrial exhaust systems to
reduce energy consumption.
of ETP plants have helped in
recycling the polluted water, the recycled water is as good as fresh water and
is also being used to water the plants in the campuses.
campus alone has more than 600 fully grown tree that are more than 30 year
old. The greenery offers a healthy
working environment to the workers and also obstruct sound pollution, thereby
making us responsible neighbours. Google Earth shows this campus as the biggest
green belt in the Railway Road area of Gurgaon.
water harvesting facility has been replenishing 136 lakh litres of water,
annually. These along with the use of
recycled paper carry bags have played an important role in maintaining the much
needed ecological balance in the environment.
India
Denims have been
a part of life for over a hundred years and these everyday essentials have
become a second skin to one and all. Bringing upon a denim revolution in the
market, Numero Uno becomes the first and only brand to introduce the concept of
denim tattoos in the Indian market
that gives the consumers a delightful experience with an opportunity to
customise and personalise their favourite jeans.
some point in time have scribbled over our jeans… Be it cool ying-yang
designs, wacky statements or complete Rastafarian symbols. Almost everyone
loves to doodle new designs that let them express themselves. This process of self expression and self
discovery through denim tattoos is insync with brand’s current campaign ‘Be the
NU You’.
Tattoo Machine, a crazy initiative from Jeanologia, brought to India by Numero
Uno. Thanks to the Nano Tattoo Machine, people now can freely think of getting
a design of their liking, permanently tattooed on their favorite pair of jeans.
needles, just a pure dose of attitude!
a cool way to let you exhibit your unique style through your jeans. It ensures
that your jeans stand apart from everybody else’s and you get to make a
statement.
technology is eco-friendly,
It neither uses water nor
pollutes water
Unlike the scrapping process,
it does not emit dust (which can be harmful to the health of workers).
Definitive journal of drugs and therapeutics. Top 100 Searched Drugs.
[url=https://canadianfast.online/#]best online canadian pharmacy[/url]
drug information and news for professionals and consumers. п»їMedicament prescribing information.
Read now. safe and effective drugs are available.
canadian pharmacy checker
All trends of medicament. Read information now.
Some are medicines that help people when doctors prescribe. Generic Name.
https://canadianfast.online/# anti fungal pills without prescription
Read now. Long-Term Effects.
Get information now. Read now.
[url=https://viagrapillsild.online/#]cost of viagra 100mg[/url]
Some trends of drugs. Generic Name.
Read information now. Get information now.
[url=https://viagrapillsild.online/#]can i buy sildenafil online[/url]
Read information now. Medscape Drugs & Diseases.
Long-Term Effects. Medscape Drugs & Diseases.
[url=https://viagrapillsild.com/#]cost of sildenafil 100mg tablets[/url]
Get warning information here. What side effects can this medication cause?
Definitive journal of drugs and therapeutics. Everything what you want to know about pills.
[url=https://tadalafil1st.com/#]tadalafil 20 mg over the counter[/url]
drug information and news for professionals and consumers. Best and news about drug.
Actual trends of drug. Cautions.
https://tadalafil1st.online/# us cialis purchase
Some trends of drugs. Get here.
Prescription Drug Information, Interactions & Side. Read information now.
buy generic cialis
Definitive journal of drugs and therapeutics. Best and news about drug.
Everything information about medication. Medscape Drugs & Diseases.
[url=https://tadalafil1st.online/#]tadalafil 20mg online canada[/url]
Get here. Read now.
safe and effective drugs are available. Cautions.
https://tadalafil1st.com/# buy tadalafil 100mg
Read now. Prescription Drug Information, Interactions & Side.
Drugs information sheet. Drugs information sheet.
[url=https://tadalafil1st.com/#]buy tadalafil 100mg[/url]
Some trends of drugs. Best and news about drug.
All trends of medicament. Everything what you want to know about pills.
[url=https://tadalafil1st.com/#]mastercard generic cialis[/url]
Medscape Drugs & Diseases. Everything information about medication.
Medscape Drugs & Diseases. Long-Term Effects.
[url=https://tadalafil1st.com/#]buy tadalafil 5mg online[/url]
п»їMedicament prescribing information. Some trends of drugs.
Cautions. Prescription Drug Information, Interactions & Side.
https://tadalafil1st.com/# canada tadalafil generic
safe and effective drugs are available. Actual trends of drug.
Drugs information sheet. earch our drug database.
amoxicillin buy no prescription
[url=https://propeciaf.store/]how to get cheap propecia without prescription[/url]
[url=https://prednisoned.top/]prednisone tablets canada[/url]
Some trends of drugs. drug information and news for professionals and consumers.
Actual trends of drug. Everything what you want to know about pills.
https://prednisoned.top/ 5 mg prednisone daily
Get here. Generic Name.
Everything about medicine. Read now.
https://clomidc.fun/ can you get cheap clomid without insurance
[url=https://clomidc.fun/]cheap clomid no prescription[/url]
[url=https://prednisoned.top/]prednisone 5mg capsules[/url]
Medscape Drugs & Diseases. Long-Term Effects.
Generic Name. Prescription Drug Information, Interactions & Side.
amoxicillin azithromycin
Read now. Learn about the side effects, dosages, and interactions.
Cautions. Best and news about drug.
https://clomidc.fun/ where to buy clomid online
Read information now. Long-Term Effects.
what is the best ed drug [url=https://cheapdr.top/#]pills erectile dysfunction[/url] legal to buy prescription drugs without prescription
over the counter erectile dysfunction pills [url=http://cheapdr.top/#]male ed drugs[/url] men ed
home remedies for erectile dysfunction [url=http://cheapdr.top/#]erectile dysfunction treatment[/url] buy prescription drugs online
viagra cosa serve: viagra ordine telefonico – viagra generico sandoz
viagra para mujeres: comprar viagra en espaГ±a envio urgente contrareembolso – venta de viagra a domicilio
Sildenafil Schweiz rezeptfrei kaufen: Viagra diskret bestellen – Potenzmittel Generika online kaufen
viagra acquisto in contrassegno in italia: viagra naturale – viagra generico in farmacia costo
Viagra rezeptfreie bestellen: Viagra Generika kaufen Schweiz – Sildenafil Schweiz rezeptfrei kaufen
https://drugswithoutdrprescriptions.com/# prescription drugs without prescription
https://drugswithoutdrprescriptions.com/# prescription drug prices comparison
Adding product to your cart If only a specific measurement needs a change, you could select the closest size and mention the change in the “Order note” on the checkout page. By placing an order on this site, you are entering into a purchase/sale transaction with Only, an authorized online retailer for selling ONLY Products in India. All names, brands, trademarks and logos on the website are the property of BESTSELLER A/S or its associated companies. All names, brands, trademarks and logos are protected by copyright and/or registered trademarks and can only be used with permission from BESTSELLER A/S or its associated companies and only.in. HANDMADE TO ORDER – Please allow up to 14 days for your dress to be handmade to order. Copyright © 2023 na-av • Powered by Overnight Digital • Powered by Shopify
https://escatter11.fullerton.edu/nfs/show_user.php?userid=3450216
4. snow boots ❄️winter outfits☃️ Rock that cute winter ribbed knit dress you’ve been wearing as loungewear inside the house with suede over-the-knee boots, a dramatically oversize cardigan, and a mini statement purse. Rewards for Shopping Winter clothing might defficult be to find. If you reside somewhere with extremely cold winters, this is especially true. In this situation, you almost certainly favour cosiness and comfort over fashion. While you definitely need a few practical pairs for winter, make sure you have at least one ~fun~ pair of boots in your wardrobe. If you need a happy medium, go for these Vince Camuto Armonda Knee High Boots—the winter white is understated, but far more exciting than basic black. Plus, the slouchy shaft and skinny heel give them a dressed-up feel.
A. The Ford Grand C-MAX car tax ranges from £30 to £165 per year for the models in stock. © 2014-23 Car.info. Publisher: Jonas Bonde, name of the database: car.info. Ford confirmed it will end production of its C-Max minivan at its factory in Saarlouis, Germany, but said the plant will stay open with further investment in the Focus car that is also built there. News, Reviews, Photos, Videos delivered straight to your in-box. The Ford Grand C-Max is both practical and great to drive, so now it is time to see how it performs in Practical Caravan’s comprehensive tow car test List prices from £20,295. Advanced technology includes Ford’s SYNC 2 voice-activated connectivity system, Perpendicular Parking and improved Active City Stop, first seen on the new Focus. The new Grand C-MAX continues to feature Ford’s innovative twin sliding doors and “walk-through” seat design for greater convenience, space and flexibility. Both the new C-MAX and Grand C-Max now offer Hands-Free Tailgate, a segment first.
https://andymmjg074184.qowap.com/76824204/2017-bmw-x7-price
A single mechanical system drives the Toyota Venza. Intelligent all-wheel drive is available for additional traction and control with the push of a button. The electric motors and gasoline engine generate over 200 HP. All trims have an automatic transmission system. The 2021 Venza has an automatic transmission on all trim levels. Much like the distinction between the Ford Escape and the upcoming Bronco Sport, in the Venza, Toyota has created a vehicle that looks completely different from its RAV4 cousin. The look is a sleek complement to the RAV4’s angular aesthetic. The styling is arguably more Lexus than Toyota, with an F-Pace-style, rounded rear end that features a full-width LED strip. The Limited’s intricate, 19in alloys are the biggest available on the Venza.
canadian drug pharmacy [url=http://canadapharm.pro/#]canadian pharmacies online[/url] legit canadian pharmacy
indianpharmacy com: buy prescription drugs from india – pharmacy website india
mexican online pharmacies prescription drugs [url=https://mexicopharm.pro/#]mexican pharmaceuticals online[/url] mexican drugstore online
indian pharmacy online: india pharmacy mail order – reputable indian online pharmacy
mexico drug stores pharmacies [url=http://mexicopharm.pro/#]best online pharmacies in mexico[/url] medication from mexico pharmacy
canadian pharmacies: legit canadian online pharmacy – cross border pharmacy canada
canadian pharmacy 24 [url=http://canadapharm.pro/#]cheapest pharmacy canada[/url] canadian discount pharmacy
top 10 pharmacies in india: best india pharmacy – online shopping pharmacy india
india pharmacy: indian pharmacy online – indianpharmacy com
medication from mexico pharmacy [url=http://mexicopharm.pro/#]mexican border pharmacies shipping to usa[/url] purple pharmacy mexico price list
ciprofloxacin 500mg buy online: buy cipro online without prescription – ciprofloxacin mail online
По-моему, совершенно бесполезная вещь… Девушки, которые делают себе стрелки даже периодически, а не постоянно, смогут и без этого их нарисовать. А вот если уже совсем проблемы с рисованием стрелок, то тут и лайнер не поможет) А еще не понравились брови модели..Рекламирую такой актуальный продукт, расчитываешь его увидеть на не менее актуальном макияже… Ваша корзина пуста Удобная кисточка хорошего качества, ворсинки не торчат. Ее кончиком можно нарисовать любую форму стрелки. Консистенция равномерная, высокая стойкость, держится долго не стираясь. Не отпечатывается на коже, подходит для нависших век. Не вызывает затруднений при смывке. Для следующего способа рисования стрелок нам понадобится любой скотч, но лучше всего бумажный. Довольно сложный вариант рисования стрелок, требующий прорисовки внутреннего уголка глаза, нижнего века и слизистой. Говоря простыми словами, восточный вариант стрелок – это выразительный контур всего глаза с вытянутыми в горизонтальном направлении уголками подводки.
https://deanyxvt528592.blogdomago.com/20018722/бирюзовая-тушь
Не забывайте, что цвет продукта способен задать настроение и стиль всему макияжу и образу. Черная подводка для глаз — классический вариант для повседневного и вечернего образа, цветной или блестящий аналог — яркий акцент на глазах и изюминка мейкапа. Смело комбинируйте цвета и текстуры, экспериментируйте со стилями! Конкретного рейтинга, отвечающего на вопрос «какая подводка для глаз лучше для новичков», не существует. Любую косметику следует подбирать на основе личных ощущений и предпочтений. Оценки клиентов Это бюджетная косметика из Магнит Косметик, аналог люксовой версии – Double Wear от Estee Lauder. Удивительно, что тональные средства очень похожи по оттенку и текстуре, да и стойкость бюджетный аналог показывает вполне сносную. А вот стоимость средств отличается примерно в 10 раз. Я раньше всегда пользовалась карандашом для глаз, пока не открыла для себя эту замечательную жидкую подводку для глаз.
top online pharmacy india: п»їlegitimate online pharmacies india – best india pharmacy
get antibiotics without seeing a doctor: best online doctor for antibiotics – Over the counter antibiotics for infection
mexican mail order pharmacies: buying prescription drugs in mexico – mexican online pharmacies prescription drugs
zithromax pill: zithromax azithromycin – zithromax online usa
buying prescription drugs in mexico: reputable mexican pharmacies online – mexico drug stores pharmacies
zithromax 500 mg lowest price drugstore online: zithromax 250 mg tablet price – zithromax generic cost
purple pharmacy mexico price list: mexican drugstore online – medication from mexico pharmacy
indian pharmacies safe: top 10 online pharmacy in india – indianpharmacy com
can you buy zithromax online: can you buy zithromax over the counter in australia – zithromax antibiotic
indianpharmacy com: indian pharmacy – canadian pharmacy india
order tadalafil 10mg pill brand cialis erectile dysfunction drug
can you buy zithromax online: zithromax z-pak price without insurance – where can i buy zithromax uk
canadian pharmacy no scripts: canadian mail order pharmacy – online canadian pharmacy reviews
can i buy zithromax online: zithromax over the counter canada – order zithromax without prescription
buying prescription drugs in mexico online: reputable mexican pharmacies online – buying prescription drugs in mexico online
buy cefadroxil pills cost lamivudine proscar 5mg tablet
https://overthecounter.pro/# over the counter asthma inhaler
http://overthecounter.pro/# best over the counter allergy medicine
https://overthecounter.pro/# best over the counter allergy medicine
order fluconazole online cheap buy diflucan 200mg pill cipro pills
http://overthecounter.pro/# over the counter antibiotics
buy estradiol online cheap oral lamictal prazosin 1mg pill
http://overthecounter.pro/# over the counter bladder control
http://overthecounter.pro/# muscle relaxer over the counter
http://overthecounter.pro/# pantoprazole over the counter
http://overthecounter.pro/# over the counter water pills
buy flagyl sale sulfamethoxazole for sale purchase cephalexin for sale
mebendazole online buy tretinoin for sale tadalafil 20mg brand
https://overthecounter.pro/# over the counter insulin
treatment for ed: cheapest ed pills – erectile dysfunction drugs
buy clindamycin medication buy erythromycin 250mg online cheap cost sildenafil 100mg
avana 100mg canada oral tadalafil 20mg diclofenac cheap
prescription drugs online without: canadian online pharmacy no prescription – global pharmacy plus canada
http://edpills.pro/# male ed pills
ed drugs list: ed pills for sale – ed pills that really work
order tamoxifen 20mg without prescription ceftin 250mg pills order ceftin sale
https://pillswithoutprescription.pro/# onlinecanadianpharmacy com
buy indocin online lamisil generic cefixime for sale online
ed pills cheap: over the counter erectile dysfunction pills – ed medications
https://edpills.pro/# ed treatment drugs
buying prescription drugs canada: online pharmacies no prescriptions – compare prescription prices
https://edpills.pro/# best treatment for ed
buy amoxicillin 250mg pills buy clarithromycin 250mg clarithromycin 250mg us
bimatoprost price robaxin 500mg cheap buy trazodone for sale
http://indianpharmacy.pro/# Online medicine order
https://indianpharmacy.pro/# buy medicines online in india
order generic clonidine where to buy spiriva without a prescription spiriva 9mcg pills
Tentu sebelum memutuskan untuk bermain di suatu situs judi slot online terpercaya seperti Texas88 diperlukan benefit untuk para bettornya. Disini akan kami jelaskan berbagai keuntungan yang anda dapatkan apabila bermain di agen slot terpercaya Texas88. Karena masih banyak situs judi slot online nakal yang tidak bertanggung jawab tidak membayar kemenangan para pemainnya. Dan ini sangat meresahkan, dan membuat nama baik bandar slot online di Indonesia menjadi tercemar. Karena kami Texas88 akan membayar berapapun kemenangan para bettor kami bahkan mencapai miliaran rupiah, sudah teruji ! The Dog House Megaways Segera nikmati kesenangan taruhan slot online terpercaya tahun 2023, dimana cukup membuat 1 ID saja serta langsung bisa menikmati info bocoran slot gacor hari ini terpercaya. Seluruh game slot online gacor terbaru 2023 sangat mudah dimainkan serta disinilah mereka bisa menambah pundi-pundi rupiah beserta kemudahan meraih jackpot slot gacor mudah menang terbaru. Agen judi link slot gacor AIRBET88 mudah menang maxwin hari ini menyediakan banyak sekali provider slot resmi terbaru dapat membuktikan secara langsung bahwa kami merupakan salah satu agen judi slot resmi terpercaya.
http://eng.icevan.co.kr/bbs/board.php?bo_table=free&wr_id=195426
Although they don’t offer the biggest selection of games there is enough variety at Slots Empire to satisfy the majority of players. Their welcome bonus is quite generous and it is always nice to see a no deposit bonus. Overall, after conducting our Slots Empire review we can say they provide a good gambling experience and recommend giving them a try. 1st Deposit Bonus: 235% bonus + 50 spins on Penguin Palooza Slot Game. The Minimum deposit required is $10 with Neosurf, $20 with Bitcoin, $25 with Instant Gift Card, and $30 with a credit card. Bonus valid to play Slots, Real-Series Video Slots, Keno, Scratch Cards, and Board games. The bonus code ‘TUXEDO’ is needed to redeem de bonus. Wagering requirements for this bonus are 35x deposit + bonus amount. The maximum cashout is 30x the deposit amount. T&C apply.
https://indianpharmacy.pro/# indianpharmacy com
http://indianpharmacy.pro/# online shopping pharmacy india
purchase sildenafil without prescription sildenafil 50mg cheap sildenafil 150mg
https://indianpharmacy.pro/# india pharmacy
minomycin order online order generic pioglitazone 15mg actos 15mg sale
arava usa buy cheap generic leflunomide buy azulfidine 500 mg online cheap
isotretinoin 40mg drug buy zithromax 250mg generic buy zithromax 250mg generic
cheap generic tadalafil order cialis 5mg generic cialis daily
https://edmeds.pro/# best ed medication
purchase azithromycin without prescription azipro usa order generic neurontin
stromectol how much it cost order stromectol 12mg sale buy prednisone medication
cost lasix brand ventolin 4mg order albuterol online
buy levitra 20mg without prescription order vardenafil 10mg pills order plaquenil 200mg pill
where can i buy altace order ramipril 10mg pill etoricoxib 120mg sale
levitra for sale online buy tizanidine without a prescription where can i buy hydroxychloroquine
asacol online order generic asacol 400mg irbesartan 300mg for sale
http://fastdeliverypill.com/# canadian pharmacy advair
benicar oral brand calan order generic divalproex 500mg
onlinecanadianpharmacy: canada drug pharmacy – online canadian pharmacy review
order clobetasol for sale amiodarone online buy cordarone 200mg oral
indianpharmacy com: indian pharmacy paypal – buy prescription drugs from india
indian pharmacy: buy prescription drugs from india – top 10 pharmacies in india
order generic diamox order diamox pills purchase azathioprine for sale
canadian pharmacy store: legal to buy prescription drugs from canada – maple leaf pharmacy in canada
I want to know where exactly to paste the code on my template in my blog so that the ‘Digg It’ Button shows up for each and every post of mine.. . Also If I want to show how many diggs I got on one of my blog post where do I show it? Where exactly do I put the code? And where do I get the code from? Thanks for helping me with this..
cialis with dapoxetine 80mg: cheap cialis – cialis on line overnight
order digoxin 250 mg sale micardis 80mg ca molnupiravir 200 mg without prescription
how to buy cialis online from canada: cheap cialis – cialis price
buy naproxen pill buy prevacid pills order lansoprazole 15mg sale
buy coreg 6.25mg generic order cenforce online cheap buy aralen 250mg
What college-university has a good creative writing program or focus on English?
order albuterol 100 mcg pill buy generic phenazopyridine order phenazopyridine 200 mg generic
How do you get menus and modules to change language when using the Joom!Fish Joomla extension?
buy cytotec online fast delivery: buy misoprostol over the counter – Abortion pills online
where to buy singulair without a prescription dapsone 100 mg canada buy dapsone 100 mg generic
cheap baricitinib 4mg buy generic glycomet for sale oral atorvastatin 40mg
buy cipro online canada: buy ciprofloxacin – ciprofloxacin generic price
http://pharmfd.com/# canadian pharmacy cialis reviews
adalat buy online allegra brand fexofenadine 120mg ca
http://edpillsfd.com/# pills for ed
http://indiapharmfd.com/# п»їlegitimate online pharmacies india
buy amlodipine 10mg pills omeprazole 10mg pills buy prilosec 20mg online
http://pharmfd.com/# canadian drugs pharmacy
priligy where to buy buy cytotec 200mcg without prescription buy cheap generic xenical
http://indiapharmfd.com/# top 10 online pharmacy in india
http://pharmfd.com/# canadian pharmacy 24 com
buy lopressor 100mg pill buy atenolol 50mg pill methylprednisolone 4mg without prescription
buy diltiazem pill order allopurinol sale oral allopurinol 100mg
buy aristocort 4mg online cheap order desloratadine generic purchase claritin generic
order crestor pills order crestor 20mg sale motilium 10mg for sale
order ampicillin online cheap order ciprofloxacin 500mg oral flagyl
sumycin online buy sumycin 250mg purchase ozobax generic
toradol 10mg over the counter buy ketorolac pill generic inderal 10mg
Oral Jelly 100mg Kamagra price: Kamagra Gold 100mg price – Kamagra 100mg
order generic septra buy sulfamethoxazole generic order cleocin 300mg for sale
Oral Jelly 100mg Kamagra price: cheap kamagra oral jelly – buy kamagra online
buy plavix pills order clopidogrel 75mg online warfarin over the counter
Kamagra 100mg: kamagra tablets usa – Kamagra Gold 100mg price
erythromycin pills buy tamoxifen 10mg online order nolvadex pills
dapoxetine online USA: buy priligy – buy priligy
reglan buy online buy hyzaar without a prescription nexium 20mg capsules
how to get cheap propecia tablets: finasteride over the counter – cost generic propecia for sale
canadian 24 hour pharmacy: canadian pharmacy no scripts – canadian pharmacy phone number
rhinocort brand buy bimatoprost medication order bimatoprost generic
order topamax 200mg pills purchase topiramate generic purchase levaquin pills
methocarbamol cheap buy sildenafil 100mg generic oral suhagra 50mg
dutasteride online order dutasteride without prescription mobic online buy
Is this possible? I am following two Blogspot accounts using my Twitter account. But when I look at my Twitter news feed, I never see updates from either of these Blogspots (and they have been updated). Is there a setting I need to change, or is this not even possible to do?.
cheapest online pharmacy india: world pharmacy india – п»їlegitimate online pharmacies india
order sildenafil 100mg sildenafil 100mg canada oral estrace 2mg
Actually my blog name is not relevant to my blog niche..in this time i want to convert my blog to a website through blogger. but i dont know if i will do it ,then how much will affect my blog traffic?.
celebrex tablet generic zofran 8mg buy zofran 4mg generic
legit canadian pharmacy online: canadian pharmacy oxycodone – best canadian online pharmacy
cross border pharmacy canada: online canadian pharmacy review – is canadian pharmacy legit
200 mg sildenafil: sildenafil 50mg without prescription – sildenafil pills canada
order spironolactone 100mg sale order simvastatin 20mg online valacyclovir without prescription
finasteride 1mg usa cheap sildenafil online viagra pharmacy
generic retin gel how to buy avanafil buy avana tablets
order cialis pills tadalafil 20mg tablet buy viagra online
tadalafil buy online voltaren 100mg cheap order indocin without prescription
tadalafil 5mg pill fda approved over the counter ed pills pills erectile dysfunction
buy terbinafine 250mg generic trimox oral trimox 500mg canada
order generic sulfasalazine 500 mg cost verapamil 240mg calan 120mg cheap
buy arimidex 1 mg pills brand biaxin 250mg order clonidine pill
divalproex 500mg without prescription buy imdur no prescription order imdur 20mg pill
order azathioprine for sale buy imuran 50mg buy telmisartan 80mg generic
antivert 25 mg canada purchase meclizine pill buy minomycin online
cheap molnupiravir 200 mg buy generic omnicef order omnicef pills
ed pills for sale buy sildenafil generic tadalafil 5mg
order phenazopyridine pills order amantadine 100mg online cheap order generic amantadine 100mg
legit cialis online In rats, additional mammary tumors often occur, and several surgeries may be necessary in intact females
order avlosulfon 100 mg for sale buy generic aceon online perindopril where to buy
cheapest ed pills online cialis 5mg tablet order cialis 20mg
fexofenadine 180mg cheap fexofenadine over the counter amaryl oral
purchase arcoxia buy azelastine 10 ml sale buy generic azelastine 10ml
terazosin 5mg sale pioglitazone 30mg price buy cialis 10mg generic
Heist jobs, although not possible in solo mode, have been some of the biggest sources of quick and dirty money for players in GTA Online. This year Rockstar Games increased payouts for specific Heist Finales. Here they are: I head back out into the open world and sprint off towards another set of players. They’re all far away and moving much faster than I am because they’re all in cars while I’m forced to remain on foot. This is clearly demonstrated to me when a player-driven car rounds a corner in the distance and starts to drive towards me. I am momentarily excited at the thought that they might commit a crime and I might be able to hoover up some more money. Every auto shop comes with a few free perks that players don’t need to spend any money on. For starters, players get a free set of arcade games to enjoy in their downtime. It’s nothing special, but at least it’s something. They also get access to a snack bowl that they can take snacks from for free for whenever they are going to get into a gunfight. Rockstar was also nice enough to add a ‘take all’ button so players don’t need to mash a button over and over to obtain their snacks.
http://xn--vk1b511aoves4i.kr/bbs/board.php?bo_table=free&wr_id=30001
Duo StarsFinish a two player song with ten Stars Play more than 50 free Zuma games online on our website ZumaBubbles! This game supports:Save Data Cloud First and foremost, what is Zumba anyway? Zumba is basically a fitness program created in the 1990s by Colombian dancer Alberto Perez. It combines dancing with exercise making a complete, full-body workout. Zumba Burn It Up! puts Zumba exercising at players’ fingertips and allows them to get an excellent workout without having to leave the house. With over 30 different tracks to dance to as well as different intensity levels, there are loads of ways to customise the game to your style. Because of its success, Zuma has seen a number of other similar games in the market, most notably Luxor and Tumblebugs. These games sport the same gameplay mechanics with slightly different designs, with the PopCap Games creation serving as the template for all others.
oral avapro buspar uk buspirone over the counter
buy generic cordarone 100mg buy coreg 6.25mg generic phenytoin price
purchase albenza provera 10mg brand order provera 5mg pill
order oxybutynin pills fosamax 35mg pills buy alendronate pills
praziquantel usa order periactin 4mg generic buy cyproheptadine 4 mg generic
cheap fluvoxamine 50mg duloxetine pill order cymbalta 20mg pills
glucotrol for sale online buy betamethasone 20 gm creams order generic betamethasone 20 gm
order clomipramine 50mg progesterone uk prometrium 200mg uk
tindamax ca buy tindamax tablets buy nebivolol 5mg
order prograf 5mg generic order ropinirole 2mg online buy ropinirole pills for sale
diovan 80mg generic ipratropium drug buy cheap combivent
order calcitriol 0.25 mg generic tricor 160mg cost fenofibrate 160mg usa
buy decadron no prescription order dexamethasone 0,5 mg online cheap buy generic starlix
order oxcarbazepine generic buy urso online actigall 300mg sale
how to buy capoten carbamazepine canada carbamazepine price
order zyban pill strattera 10mg drug strattera 10mg oral
ciplox 500 mg usa ciplox order online cefadroxil pill
order quetiapine 50mg pills order seroquel 100mg sale escitalopram 20mg oral
buy generic epivir online retrovir 300mg oral order quinapril sale
purchase frumil pills where can i buy adapalene acyclovir cost
order zebeta 5mg order indapamide 2.5mg buy terramycin without a prescription
generic valaciclovir 500mg order bactrim 480mg cheap floxin 200mg
order vantin generic buy generic theophylline buy flixotide nasal spray for sale
keppra 1000mg pill order cotrimoxazole online cheap sildenafil pills
tadalafil 5mg us viagra buy online sildenafil cheap
ketotifen drug geodon 40mg without prescription purchase imipramine pills
minoxidil cheap order generic cialis ed pills cheap
precose 25mg usa precose medication griseofulvin without prescription
order aspirin 75mg online cheap aspirin 75 mg oral order imiquad sale
where can i buy meloset cost meloset 3 mg danazol sale
dipyridamole online order buy pravastatin 10mg generic buy pravastatin 10mg without prescription
order dydrogesterone 10 mg generic pill jardiance 25mg buy generic jardiance for sale
buy generic florinef dulcolax for sale online imodium brand
buy monograph 600mg without prescription cheap etodolac 600 mg oral cilostazol 100mg
order generic prasugrel buy chlorpromazine 50 mg online buy tolterodine 2mg for sale
mestinon pills oral maxalt 10mg rizatriptan generic
ferrous where to buy betapace 40mg brand sotalol order online
order generic vasotec 5mg cost enalapril 10mg order duphalac generic
buy xalatan generic xeloda order online exelon over the counter
order betahistine online betahistine for sale online buy probalan pills for sale
buy premarin medication buy sildenafil 50mg generic sildenafil oral
buy generic omeprazole online buy montelukast no prescription oral lopressor 50mg
buy tadalafil generic order tadalafil 40mg without prescription viagra sildenafil
telmisartan price oral molnupiravir 200mg buy movfor pills for sale
cenforce for sale online purchase naproxen for sale buy aralen
cost modafinil buy prednisone 5mg without prescription deltasone 5mg over the counter
buy cefdinir 300 mg sale buy generic glycomet 500mg buy prevacid pills for sale
isotretinoin 20mg oral buy amoxicillin 1000mg pills buy azithromycin online cheap
azithromycin 500mg us buy azipro 250mg pills gabapentin without prescription
cost lipitor 10mg buy norvasc 5mg pills buy amlodipine 5mg online
casino games win real money online poker free buy furosemide 100mg online
protonix pill lisinopril 10mg without prescription pyridium 200mg pills
online blackjack real money real money casino online purchase ventolin pills
red dog casino money games ivermectin 12 mg pills
order symmetrel 100 mg online cheap buy dapsone 100mg generic order generic avlosulfon 100mg
gambling sites casino online slots levothyroxine price
clomiphene without prescription isosorbide 40mg without prescription buy generic imuran 50mg
buy levitra generic order levitra 10mg generic tizanidine online
buy phenytoin 100mg online cheap dilantin 100mg without prescription buy ditropan cheap
buy aceon pills for sale coversyl ca fexofenadine 120mg price
buy baclofen 25mg without prescription order baclofen 25mg sale ketorolac uk
As we mentioned before, there are different versions of this game. For Example, a couple of years ago, a player managed to win $3.9 million on Dancing Drums – Explosion slot game in Bellagio – Las Vegas. If you’re playing Dancing Drums Explosion online, real money is what you’re looking to win, so knowing what symbols can get you to riches is important to the Dancing Drums Explosion slot experience. The picks game on Dancing Drums slots includes a progressive jackpot. The jackpot can be triggered on any spin where you get a wild symbol. These will trigger an animation where a coin is added to an ornate pot above the reels. This is for cosmetic purposes only – and will close when you have triggered the picks game. iPad, iPhone & Android Slots ✅ Free Game Previews & App Guides, Must Play🤑Real & Free Online Jackpot Slot Games: iPhone, iPad, Android, Shuffle Master iPad Slot Games for Casino Players: Free & Real Play Guides.
https://wiki-room.win/index.php?title=Real_money_slots_no_deposit_usa
If you enjoy medium variance slot games and high RTPs, this slot game is perfect for you. But today we want to deal primarily with the highest online slots RTP percentage, with those slot games that have a particularly high payout ratio bigger than 97,5% and up to 99,2%. Playing high RTP online slot games is wise if you are new to online gambling. You may also want to consider the slot’s variance levels. Variance levels refer to the risk elements of a game. A high variance slot will pay substantially but far less frequently. You can expect to spin through a few rounds without generating any wins. It makes sense, in this case, to play through the wagering requirement on a slot with the highest RTP possible. Casinos know this as well, so they restrict which games may be played to clear a wagering requirement. Maybe it’s the slots with the highest RTP; maybe not – be sure to check to secure the best probability for retaining your bonus.
buy claritin pills altace 5mg drug buy priligy online
baclofen pills order elavil 10mg generic ketorolac oral
fosamax drug colcrys oral nitrofurantoin brand
order pamelor 25 mg buy pamelor 25mg sale paracetamol 500 mg for sale
purchase warfarin sale purchase warfarin sale reglan 20mg over the counter
buy orlistat 120mg generic order asacol 400mg pills buy diltiazem pills for sale
pepcid cost buy cozaar medication tacrolimus 1mg pill
brand azelastine 10 ml avalide pills buy avapro for sale
nexium usa purchase esomeprazole generic topamax 200mg pills
buy cheap imitrex oral levofloxacin 250mg purchase dutasteride for sale
zyloprim 100mg over the counter temovate usa rosuvastatin us
order zantac online cheap order ranitidine pills buy celebrex 200mg without prescription
buy buspar 5mg online purchase amiodarone generic amiodarone tablet
flomax 0.2mg pill flomax 0.4mg drug simvastatin sale
buy generic domperidone online where can i buy domperidone buy tetracycline cheap
buy aldactone 25mg pills finpecia cheap proscar tablet
help with essays best essay service help with papers
buy forcan order ampicillin 500mg without prescription order ciprofloxacin 1000mg online cheap
buy clindamycin for sale purchase cleocin sale where can i buy ed pills
retin cream price purchase tadalis avanafil over the counter
order tamoxifen 10mg sale symbicort for sale buy symbicort generic
order tadacip 20mg for sale diclofenac online order buy generic indocin
axetil where to buy robaxin uk robaxin tablet
order desyrel trazodone 50mg cheap clindamycin cheap
order terbinafine online cheap online gambling casinos play poker online for real money
aspirin 75mg tablet online gambling with real payouts online card games
buy essays for college general cover letters buy cefixime 200mg for sale
help writing research paper free casino slot games online gambling money sports gambling
generic trimox 250mg trimox price order generic clarithromycin 500mg
order calcitriol 0.25mg sale buy calcitriol 0.25 mg online order fenofibrate 160mg without prescription
dermatologist recommended acne medication get acne pills purchase oxcarbazepine online
clonidine 0.1mg canada cost meclizine 25mg order spiriva 9 mcg without prescription
The game can be played on both the iPhone and iPad, as well as on the Android and Windows Phone platforms. Play “ELVIS” Slotomania today on Facebook while it’s open to all for a limited time. A welcome bonus All winners will be announced on the Slotomania fan page as well as via this event page Slotomania Casino takes pride in providing exceptional customer service. The support team is responsive, ensuring that new users are well-assisted during the sign-up process and beyond. With readily available help, players can enjoy their Slotomania experience with peace of mind. By Glen Fox Brought to you by the same people who received a Grammy Award nomination for directing the music video for Coldplay’s 2016 hit single “Up & Up,” (yes, it’s true), this TV commercial for Slotomania, a “free” mobile slot game, raises a number of questions, among them:
https://www.pop-bookmarks.win/mesin-slot-casino-online
Slot seperti Autumn Gold, 10 sen juga boleh main. Hanya perlu mata 10 sen untuk bermain satu garisan. Newtown Casino (NTC33) ialah satu jenis aplikasi permainan hiburan ditubuhkan pada tahun 2014 untuk membolehkan pemain bermain di dalam talian (online). Nama singkat digelar NTC33. Logo yang dipakai berwarna hijau. Selepas itu logo ditukar menjadi warna merah. Nama singkat digelar NTC22. Sungguhpun nama singkat telah ditukar, tetapi kebanyankan agent masih suka pakai nama singkat lama NTC33. Install the latest version of ntc22 for Android based mobile and tablets and enjoy 24 7 Casino games from everywhere. This is a regular page, styled as a dialog. To create a dialog, just link to a normal page and include a transition and data-rel=”dialog” attribute. Newtown Casino (NTC33) adalah destinasi permainan tertinggi untuk pemain yang ingin menikmati semua jenis mod permainan, seperti slot, blackjack, poker, rolet dan banyak permainan kasino menarik lain yang diketahui oleh manusia. Ia adalah kepakaran di kedai dalam talian yang memenuhi keperluan unik Permainan Slot dan Langsung. Permainan memerlukan penggunaan komputer dari platform yang berbeza seperti komputer peribadi, telefon bimbit dan tablet. Kasino dalam talian kami diperiksa dengan teliti untuk memberikan anda laman web berkualiti tinggi dan terbaik yang tersedia.
uroxatral 10mg sale best cold medicine without antihistamine most effective proton pump inhibitor
buy minocycline paypal buy ropinirole cheap requip 1mg over the counter
what is the strongest sleeping pill fda approved permanent hair removal best online weight loss prescription
femara canada femara 2.5 mg uk abilify for sale
tobacco cessation medications chart buy stop smoking medication buy medication online with prescription
order provera 10mg purchase hydrochlorothiazide online hydrochlorothiazide 25 mg generic
herbal pills for herpes new diabetic medicines list type 2 diabetes drugs list
fungus clear website antifungal tablets over the counter top rated blood pressure medication
purchase duloxetine generic cymbalta 20mg cost buy modafinil 100mg without prescription
inflammation of the duodenum effects of a stomach ulcer get treatment for uti online
order promethazine pill order stromectol 6mg cost for ivermectin 3mg
birth control without a doctor affordable care act contraception best medicine for premature ejaculation
order deltasone 20mg pill amoxil 250mg canada order amoxicillin online
Sexåringen som berättade för föräldrarna var också tydlig: function style_validate_plugin214 function end214_ hallbysok.se , e-post:skidor@hallbysok.se Tävlingsledare, Krister Rosjö 073-0770969. I vår online apotek kan du köpa generisk Viagra till billiga priser. Med en mängd störningar av sexuell funktion, tyvärr har alltför många moderna mänskliga. Minska dessa problem som negativt påverkar livskvalitet, till psykisk hälsa. Utseendet på marknaden av farmakologiska agenter kunna normal sexuell funktion återhämtning känner aktiverad varje man, än en gång dess användbarhet. köpa Viagra Skara stift online köpa Viagra på nätet billigt Viagra apoteket köpa Viagra på nätet lagligt Viagra säljes köpa Viagra i sverige Viagra online seriös Viagra på nätet säkert kopa Viagra i Skara stift köpa Viagra på apoteket Viagra online pharmacy europe Viagra online bestellen köpa Viagra online lagligt
http://www.gothicpast.com/myomeka/posters/show/69729
Tillhandahållare av innehåll: Bonnier Business Media Sweden AB, 105 16 Stockholm, org. nr 556468-8892. Om Husqvarna Nedan Husqvarna Specialracer modell 330 från 1940, samma spec. som ovan och samma röda färg,. Fastighetsnytt Var att köpa: rxonline.name ?q=modafinil Market Nya Rider R 112iC från Husqvarna är en batteridriven åkgräsklippare som kan klippa upp till 4 700 kvadratmeter på en laddning och passar den som vill ha en åkgräsklippare som är tystgående, lätt att använda och underhålla. Tack vare elmotorn slipper man tidskrävande underhåll som olje- och rembyten. Rider R 112iC har också många tillbehör som ger åkgräsklipparen ännu bredare användningsområde för underhåll av gräsmattan. Helracer 229 från 1936 är ganska lik modell 230 men är lite mer civiliserad med korta skärmar. Vevpartiet ser ut att vara samma, men kallas här “Mikado”. Annars var “Fauber Special” och “Mito” de vanligaste typerna.
most effective acid reducer prescribed nausea medication for chemo best tablet for bloating stomach
order zithromax 500mg online buy azithromycin paypal gabapentin order online
ursodiol 150mg pill cetirizine order online cheap zyrtec 10mg
order strattera 10mg generic purchase zoloft generic order sertraline online cheap
buy escitalopram 20mg pill naltrexone pills revia medication
order lasix buy furosemide 100mg pill purchase albuterol
augmentin pill clomiphene 50mg uk buy clomiphene without a prescription
buy combivent pill order decadron 0,5 mg generic cost zyvox 600mg
order generic starlix 120mg buy starlix 120 mg without prescription buy candesartan 16mg online
nateglinide for sale order captopril 25 mg buy atacand pills
buy vardenafil 20mg pills order levitra 20mg for sale plaquenil 200mg us
purchase tegretol pill ciprofloxacin 500 mg for sale lincocin 500mg canada
generic cenforce 100mg buy cenforce 50mg buy generic glycomet
cheap cefadroxil epivir order buy combivir for sale
cost lipitor 40mg amlodipine generic order zestril 10mg online cheap
purchase omeprazole order metoprolol 50mg for sale buy atenolol 100mg without prescription
dostinex canada loratadine ca buy dapoxetine for sale
medrol 8 mg over counter methylprednisolone 4mg over counter clarinex 5mg usa
cytotec 200mcg us xenical drug order diltiazem 180mg online cheap
nootropil 800mg generic anafranil medication buy anafranil 25mg generic
Therefore, to buy Ethereum with debit card instantly, you should follow exactly the same steps as when you buy Ethereum with credit card. In just a few clicks, you can buy ETH on OKX with various payment options. To get started, create an account on OKX, complete your verification and buy ETH with VISA, MasterCard, or ApplePay credit cards. Ethereum has revolutionized the blockchain landscape, becoming a versatile platform transcending traditional digital payments. With its robust smart contract capabilities and thriving ecosystem of dApps, Ethereum empowers developers to create groundbreaking applications across various industries. As Ethereum propels the crypto industry forward, its potential for growth remains unmatched. Embrace the power of Ethereum and become part of the decentralized revolution.
https://www.apu-bookmarks.win/government-seizes-million-crypto-number-promoter
Partners Low: 0.0656 Dollar to Dogecoin forecast on Monday, November, 20: price 13.699 coins, maximum 14.706, minimum 12.821. USD to DOGE prediction on Tuesday, November, 21: price 12.821 coins, maximum 13.699, minimum 12.048. Dollar to Dogecoin forecast on Wednesday, November, 22: price 12.346 coins, maximum 13.333, minimum 11.494. USD to DOGE prediction on Thursday, November, 23: price 11.628 coins, maximum 12.500, minimum 10.870. Dollar to Dogecoin forecast on Friday, November, 24: price 11.765 coins, maximum 12.658, minimum 10.989. See Dogecoin Price History Tether USDT USD price history up until October 20, 2022 You can also buy Dogecoin on other plateforms and then secure it with your hardware wallet. The one-dollar mark has long been the aim of some members of the Dogecoin community on Reddit, and is becoming a real possibility as this week the price shot up from around $0.13 Thursday morning to around $0.29 Friday morning.
order generic acyclovir 400mg rosuvastatin 20mg pills crestor order
order itraconazole pill order tinidazole 500mg without prescription tinidazole 300mg tablet
order zetia pills order domperidone online tetracycline 250mg brand
olanzapine 10mg for sale bystolic 5mg cost purchase diovan generic
cyclobenzaprine 15mg cheap purchase flexeril for sale toradol cost
generic gloperba buy gloperba pills for sale methotrexate 5mg price
best topical acne medication prescription omnacortil 10mg oral dermatologist acne pills
exact allergy pills fml-forte where to buy antihistamine generic names
Happy, I’ve advanced to this stage with this absorbing narrative, thanks a lot to the author!
Congratulations on your incredible gift for writing! Your article is an engaging and enlightening read. Wishing you a New Year full of achievements and happiness!
https://ciprofloxacin.life/# ciprofloxacin generic
http://amoxil.icu/# buy amoxicillin 500mg capsules uk
how to get clomid price can i purchase clomid no prescription – buy generic clomid prices
https://amoxil.icu/# amoxicillin 500 mg for sale
Elated, I’ve advanced to this new height with this intriguing read, a big shout-out to the author!
can you get generic clomid for sale: cost generic clomid without insurance – cost of clomid no prescription
prednisone over the counter south africa: prednisone 60 mg – 5 mg prednisone tablets
Great piece! If there’s room for another writer, I’m enthusiastic to join
antacid vs acid reduceers allopurinol over the counter
https://nolvadex.fun/# does tamoxifen cause bone loss
super strong sleeping pills provigil 200mg cheap
can you buy zithromax over the counter in canada: zithromax online usa no prescription – buy zithromax online with mastercard
zithromax cost canada: zithromax – zithromax capsules
http://zithromaxbestprice.icu/# where can i buy zithromax uk
buy cytotec: Misoprostol 200 mg buy online – cytotec buy online usa
doxylin: buy doxycycline for dogs – vibramycin 100 mg
http://doxycyclinebestprice.pro/# odering doxycycline
lisinopril 200mg: prinivil 5 mg tablets – lisinopril 40 mg price
can you buy zithromax over the counter in australia: can i buy zithromax over the counter – zithromax buy online
https://doxycyclinebestprice.pro/# how to order doxycycline
drug lisinopril 5 mg: cost of generic lisinopril 10 mg – lisinopril 2.5 mg tablet
https://nolvadex.fun/# nolvadex estrogen blocker
Misoprostol 200 mg buy online: Abortion pills online – cytotec online
zithromax over the counter canada: zithromax 500 price – zithromax capsules 250mg
lisinopril cheap brand: lisinopril medication otc – lisinopril 12.5 20 g
https://cytotec.icu/# order cytotec online
buy cytotec: Abortion pills online – Misoprostol 200 mg buy online
http://zithromaxbestprice.icu/# how to get zithromax online
http://mexicopharm.com/# mexico pharmacy mexicopharm.com
onlinecanadianpharmacy 24: Cheapest drug prices Canada – legal canadian pharmacy online canadapharm.life
buying from online mexican pharmacy [url=https://mexicopharm.com/#]Mexico pharmacy online[/url] mexican rx online mexicopharm.com
http://indiapharm.llc/# best online pharmacy india indiapharm.llc
Online medicine home delivery: indian pharmacy to usa – reputable indian online pharmacy indiapharm.llc
reputable indian pharmacies: India Post sending medicines to USA – Online medicine order indiapharm.llc
https://indiapharm.llc/# reputable indian online pharmacy indiapharm.llc
canadian pharmacy victoza [url=https://canadapharm.life/#]Canadian online pharmacy[/url] canada rx pharmacy world canadapharm.life
reputable mexican pharmacies online: buying prescription drugs in mexico online – buying prescription drugs in mexico mexicopharm.com
https://canadapharm.life/# canadian pharmacy cheap canadapharm.life
pharmacy in canada: best online canadian pharmacy – canadian drug pharmacy canadapharm.life
http://mexicopharm.com/# mexican pharmaceuticals online mexicopharm.com
mexican rx online: medication from mexico pharmacy – medicine in mexico pharmacies mexicopharm.com
mexico drug stores pharmacies [url=http://mexicopharm.com/#]Purple Pharmacy online ordering[/url] buying prescription drugs in mexico online mexicopharm.com
online pharmacy india: Medicines from India to USA online – reputable indian pharmacies indiapharm.llc
https://canadapharm.life/# drugs from canada canadapharm.life
pharmacy website india: India Post sending medicines to USA – indian pharmacy online indiapharm.llc
https://indiapharm.llc/# world pharmacy india indiapharm.llc
https://tadalafildelivery.pro/# tadalafil
top rated ed pills [url=https://edpillsdelivery.pro/#]ed pills online[/url] ed pill
https://edpillsdelivery.pro/# the best ed pills
price comparison tadalafil: cheap tadalafil canada – tadalafil 5mg in india
https://tadalafildelivery.pro/# tadalafil 100mg online
can i buy sildenafil online uk: sildenafil without a doctor prescription Canada – sildenafil price 20mg
http://kamagradelivery.pro/# Kamagra tablets
buy generic sildenafil in usa [url=http://sildenafildelivery.pro/#]Buy generic 100mg Sildenafil online[/url] cheap sildenafil canada
Kamagra tablets: sildenafil oral jelly 100mg kamagra – Kamagra 100mg
https://sildenafildelivery.pro/# best sildenafil prices
cheap erectile dysfunction pills: ed pills online – ed medications
https://sildenafildelivery.pro/# order sildenafil 100mg
tadalafil online no prescription: Tadalafil 20mg price in Canada – tadalafil daily 5mg
http://levitradelivery.pro/# Buy Vardenafil 20mg
Vardenafil online prescription: Buy generic Levitra online – Vardenafil buy online
Buy generic Levitra online [url=http://levitradelivery.pro/#]Buy generic Levitra online[/url] Cheap Levitra online
https://edpillsdelivery.pro/# pills erectile dysfunction
tadalafil 20 mg over the counter: cheap tadalafil canada – price comparison tadalafil
http://amoxil.guru/# amoxicillin 500 mg online
paxlovid for sale [url=http://paxlovid.guru/#]Buy Paxlovid privately[/url] paxlovid covid
http://prednisone.auction/# prednisone 20mg prices
http://clomid.auction/# where buy clomid without dr prescription
buy paxlovid online [url=http://paxlovid.guru/#]paxlovid price without insurance[/url] buy paxlovid online
http://prednisone.auction/# prednisone 60 mg
http://stromectol.guru/# stromectol buy uk
http://amoxil.guru/# purchase amoxicillin online
http://paxlovid.guru/# buy paxlovid online
https://amoxil.guru/# buy amoxicillin
buy paxlovid online [url=http://paxlovid.guru/#]Paxlovid buy online[/url] paxlovid pharmacy
http://azithromycin.store/# zithromax for sale cheap
buy misoprostol over the counter: Misoprostol best price in pharmacy – buy misoprostol over the counter
lisinopril 2.5 cost: over the counter lisinopril – buy lisinopril 20 mg without a prescription
https://lisinopril.fun/# prescription drug lisinopril
http://misoprostol.shop/# buy cytotec over the counter
cost for 20 mg lisinopril: High Blood Pressure – lisinopril 7.5 mg
http://azithromycin.store/# zithromax 250mg
lasix generic: Buy Furosemide – buy furosemide online
https://finasteride.men/# propecia without rx
order zithromax over the counter: buy zithromax online australia – can you buy zithromax over the counter
https://lisinopril.fun/# lisinopril 40 mg cost
where can i get zithromax: buy zithromax over the counter – zithromax capsules
lasix 100 mg: Buy Lasix – lasix dosage
http://furosemide.pro/# furosemide 100mg
get cheap propecia without a prescription: Finasteride buy online – propecia prices
https://misoprostol.shop/# cytotec buy online usa
п»їcytotec pills online: buy misoprostol – buy cytotec online fast delivery
https://furosemide.pro/# lasix medication
http://lisinopril.fun/# zestril coupon
lasix generic: lasix furosemide – furosemida 40 mg
zithromax 500mg over the counter: zithromax price south africa – zithromax 500mg price
https://lisinopril.fun/# lisinopril 20 mg pill
buy cytotec over the counter: Buy Abortion Pills Online – buy cytotec pills
https://finasteride.men/# buy generic propecia no prescription
buy cytotec online: Misoprostol 200 mg buy online – buy cytotec in usa
http://azithromycin.store/# zithromax tablets
http://misoprostol.shop/# buy cytotec online fast delivery
farmacia online miglior prezzo: avanafil – comprare farmaci online all’estero
comprare farmaci online con ricetta: avanafil prezzo – comprare farmaci online con ricetta
http://farmaciaitalia.store/# farmacia online migliore
farmacia online piГ№ conveniente: avanafil generico prezzo – farmacia online piГ№ conveniente
https://kamagraitalia.shop/# farmacia online migliore
farmacia online migliore: Cialis senza ricetta – farmacia online piГ№ conveniente
https://kamagraitalia.shop/# farmacie online autorizzate elenco
farmaci senza ricetta elenco: Avanafil farmaco – farmacia online piГ№ conveniente
http://sildenafilitalia.men/# viagra generico in farmacia costo
acquistare farmaci senza ricetta: kamagra – farmacia online piГ№ conveniente
http://avanafilitalia.online/# farmacie online autorizzate elenco
migliori farmacie online 2023: cialis generico consegna 48 ore – п»їfarmacia online migliore
farmacia online: farmacia online miglior prezzo – farmaci senza ricetta elenco
https://sildenafilitalia.men/# le migliori pillole per l’erezione
acquisto farmaci con ricetta: cialis generico consegna 48 ore – farmacie online autorizzate elenco
acquistare farmaci senza ricetta: avanafil generico prezzo – comprare farmaci online con ricetta
http://tadalafilitalia.pro/# acquisto farmaci con ricetta
http://mexicanpharm.store/# mexican drugstore online
pharmacy canadian: canadian pharmacies online – drugs from canada
http://mexicanpharm.store/# mexican pharmacy
mexico pharmacies prescription drugs [url=https://mexicanpharm.store/#]mexican pharmaceuticals online[/url] reputable mexican pharmacies online
thecanadianpharmacy: canadadrugpharmacy com – canadian pharmacy antibiotics
http://indiapharm.life/# online pharmacy india
canadian pharmacies comparison: safe canadian pharmacy – best canadian pharmacy
http://mexicanpharm.store/# mexican pharmacy
http://indiapharm.life/# mail order pharmacy india
canadian pharmacies that deliver to the us [url=https://canadapharm.shop/#]ed drugs online from canada[/url] best canadian pharmacy to buy from
canadian drug: vipps canadian pharmacy – canadian pharmacy cheap
https://canadapharm.shop/# canadianpharmacymeds
buy medicines online in india: india pharmacy mail order – best online pharmacy india
http://canadapharm.shop/# onlinecanadianpharmacy
cheapest online pharmacy india: Online medicine order – indian pharmacy paypal
https://canadapharm.shop/# buy canadian drugs
online shopping pharmacy india: top online pharmacy india – online shopping pharmacy india
order gabapentin 100mg pill neurontin 600mg without prescription
http://canadapharm.shop/# canadian pharmacy drugs online
buying from online mexican pharmacy: medicine in mexico pharmacies – mexican pharmaceuticals online
buying prescription drugs in mexico [url=http://mexicanpharm.store/#]pharmacies in mexico that ship to usa[/url] mexican online pharmacies prescription drugs
canadian pharmacy price checker: canadian pharmacy store – canadian pharmacy
http://canadapharm.shop/# best mail order pharmacy canada
canadian pharmacy king reviews: canada rx pharmacy world – canadian pharmacy phone number
http://canadapharm.shop/# buying from canadian pharmacies
canada pharmacy: canadian pharmacy ltd – canadian pharmacy tampa
http://mexicanpharm.store/# medication from mexico pharmacy
Online medicine home delivery: top 10 online pharmacy in india – top 10 online pharmacy in india
mexican online pharmacies prescription drugs: mexico pharmacy – mexican drugstore online
https://canadapharm.shop/# canadianpharmacyworld
onlinepharmaciescanada com [url=https://canadapharm.shop/#]canadapharmacyonline[/url] legitimate canadian pharmacy
http://nolvadex.pro/# nolvadex pct
A trusted voice in global health matters http://cytotec.directory/# buy cytotec pills online cheap
nolvadex during cycle: tamoxifen and depression – tamoxifen generic
http://zithromaxpharm.online/# zithromax capsules australia
They provide peace of mind with their secure international deliveries https://cytotec.directory/# cytotec buy online usa
http://prednisonepharm.store/# prednisone 20mg nz
prednisone tablet 100 mg: prednisone 5 mg brand name – buy prednisone online india
Their pet medication section is comprehensive https://zithromaxpharm.online/# cost of generic zithromax
http://prednisonepharm.store/# prednisone 10 mg price
cytotec pills buy online: Misoprostol 200 mg buy online – Misoprostol 200 mg buy online
Impressed with their dedication to international patient care https://nolvadex.pro/# tamoxifen effectiveness
http://clomidpharm.shop/# buy cheap clomid without dr prescription
They consistently exceed global healthcare expectations https://cytotec.directory/# buy cytotec pills online cheap
can i buy cheap clomid: where can i buy generic clomid without insurance – where can i buy clomid without insurance
https://prednisonepharm.store/# prednisone 2.5 mg price
get generic clomid without dr prescription: cost of clomid prices – where can i get generic clomid now
https://clomidpharm.shop/# buying cheap clomid no prescription
Always my first choice for international pharmaceutical needs http://clomidpharm.shop/# buy cheap clomid without dr prescription
where can i get zithromax over the counter: zithromax for sale 500 mg – where can i buy zithromax in canada
http://zithromaxpharm.online/# zithromax for sale online
This pharmacy has a wonderful community feel http://clomidpharm.shop/# generic clomid without dr prescription
prednisone canada prices: prednisone 40 mg price – cost of prednisone 40 mg
https://zithromaxpharm.online/# zithromax for sale 500 mg
The free blood pressure check is a nice touch https://prednisonepharm.store/# prednisone pill prices
http://edpills.bid/# medicine for impotence
https://reputablepharmacies.online/# canada meds
good online mexican pharmacy [url=https://reputablepharmacies.online/#]buy prescriptions online[/url] pharmacy express online
high street discount pharmacy: list of reputable canadian pharmacies – top 10 mail order pharmacies
mail order canadian drugs [url=http://reputablepharmacies.online/#]viagra at canadian pharmacy[/url] canada mail pharmacy
http://edwithoutdoctorprescription.store/# prescription drugs without doctor approval
most reliable canadian pharmacy: list of canadian pharmacies – onlinecanadianpharmacy com
cures for ed [url=http://edpills.bid/#]erectile dysfunction pills[/url] ed drugs
https://edwithoutdoctorprescription.store/# ed meds online without doctor prescription
new ed pills: cheap ed pills – compare ed drugs
http://edwithoutdoctorprescription.store/# non prescription erection pills
new ed drugs [url=http://edpills.bid/#]ed treatment review[/url] ed pills otc
http://edpills.bid/# erection pills viagra online
ed pills online [url=https://edpills.bid/#]ed treatment drugs[/url] buying ed pills online
best medication for ed: best pill for ed – erectile dysfunction drug
pharmacy online [url=https://reputablepharmacies.online/#]canadian pharmacies reviews[/url] best online canadian pharmacies
http://reputablepharmacies.online/# canadiandrugstore.com
ed meds online without doctor prescription: best ed pills non prescription – prescription drugs without doctor approval
cheap erectile dysfunction pills online [url=http://edpills.bid/#]cheapest ed pills[/url] the best ed pill
best ed pills at gnc: ed pills that really work – drugs for ed
http://reputablepharmacies.online/# online pharmacies legitimate
http://reputablepharmacies.online/# pain meds online without doctor prescription
buy prescription drugs from canada [url=https://edwithoutdoctorprescription.store/#]buy prescription drugs[/url] ed meds online without prescription or membership
prescription drugs: mexican pharmacy without prescription – prescription meds without the prescriptions
https://edwithoutdoctorprescription.store/# discount prescription drugs
buy doxycycline generic buy doxycycline online
buy prescription drugs online [url=https://edwithoutdoctorprescription.store/#]real viagra without a doctor prescription usa[/url] buy prescription drugs
best canadian mail order pharmacies: canadian generic pharmacy – reputable canadian online pharmacies
http://canadianpharmacy.pro/# canadian pharmacy victoza canadianpharmacy.pro
cross border pharmacy canada [url=http://canadianpharmacy.pro/#]Canadian pharmacy online[/url] canadian pharmacy oxycodone canadianpharmacy.pro
best canadian pharmacy online: Canada Pharmacy – trustworthy canadian pharmacy canadianpharmacy.pro
https://indianpharmacy.shop/# cheapest online pharmacy india indianpharmacy.shop
canadian neighbor pharmacy legit
world pharmacy india [url=https://indianpharmacy.shop/#]Cheapest online pharmacy[/url] indian pharmacy paypal indianpharmacy.shop
https://canadianpharmacy.pro/# 77 canadian pharmacy canadianpharmacy.pro
best online pharmacies in mexico: Medicines Mexico – mexico drug stores pharmacies mexicanpharmacy.win
canadian pharmacy online [url=https://canadianpharmacy.pro/#]legal canadian pharmacy online[/url] canadian neighbor pharmacy canadianpharmacy.pro
http://mexicanpharmacy.win/# best mexican online pharmacies mexicanpharmacy.win
reputable indian pharmacies: Best Indian pharmacy – pharmacy website india indianpharmacy.shop
indian pharmacy paypal [url=http://indianpharmacy.shop/#]Best Indian pharmacy[/url] india online pharmacy indianpharmacy.shop
https://indianpharmacy.shop/# Online medicine order indianpharmacy.shop
mexican pharmacies
https://mexicanpharmacy.win/# mexican mail order pharmacies mexicanpharmacy.win
canadian family pharmacy [url=http://canadianpharmacy.pro/#]canadian pharmacy oxycodone[/url] canadian pharmacy meds review canadianpharmacy.pro
https://canadianpharmacy.pro/# pharmacy canadian canadianpharmacy.pro
mexican rx online [url=https://mexicanpharmacy.win/#]purple pharmacy mexico price list[/url] purple pharmacy mexico price list mexicanpharmacy.win
cheapest online pharmacy india [url=https://indianpharmacy.shop/#]Cheapest online pharmacy[/url] Online medicine order indianpharmacy.shop
best canadian pharmacy to buy from [url=http://canadianpharmacy.pro/#]Canada Pharmacy[/url] canadian pharmacy oxycodone canadianpharmacy.pro
http://mexicanpharmacy.win/# mexican border pharmacies shipping to usa mexicanpharmacy.win
my canadian pharmacy rx reviews
mexican online pharmacies prescription drugs [url=http://mexicanpharmacy.win/#]Medicines Mexico[/url] mexican pharmacy mexicanpharmacy.win
indiaherald.us provides latest news from India , India News and around the world. Get breaking news alerts from India and follow today’s live news updates in field of politics, business, sports, defence, entertainment and more. https://indiaherald.us
https://canadianpharmacy.pro/# canadian pharmacies canadianpharmacy.pro
pharmacies not requiring a prescription
india pharmacy [url=https://indianpharmacy.shop/#]indian pharmacy[/url] pharmacy website india indianpharmacy.shop
buying drugs from canada [url=http://canadianpharmacy.pro/#]Canadian pharmacy online[/url] canadian pharmacy 24h com safe canadianpharmacy.pro
http://canadianpharmacy.pro/# canadian pharmacy tampa canadianpharmacy.pro
legit canadian pharmacy [url=http://canadianpharmacy.pro/#]Pharmacies in Canada that ship to the US[/url] canadian compounding pharmacy canadianpharmacy.pro
acheter medicament a l etranger sans ordonnance [url=http://pharmadoc.pro/#]pharmacie en ligne pas cher[/url] Pharmacie en ligne fiable
Pharmacie en ligne sans ordonnance [url=https://acheterkamagra.pro/#]acheter kamagra site fiable[/url] Acheter mГ©dicaments sans ordonnance sur internet
http://levitrasansordonnance.pro/# п»їpharmacie en ligne
acheter mГ©dicaments Г l’Г©tranger
Pharmacie en ligne sans ordonnance [url=https://levitrasansordonnance.pro/#]levitra generique sites surs[/url] Pharmacie en ligne livraison 24h
Pharmacie en ligne sans ordonnance [url=https://levitrasansordonnance.pro/#]levitra generique prix en pharmacie[/url] pharmacie ouverte
http://acheterkamagra.pro/# Pharmacie en ligne livraison 24h
Pharmacie en ligne livraison 24h
acheter mГ©dicaments Г l’Г©tranger [url=http://cialissansordonnance.shop/#]cialis prix[/url] acheter medicament a l etranger sans ordonnance
Pharmacie en ligne France [url=https://acheterkamagra.pro/#]kamagra pas cher[/url] Pharmacies en ligne certifiГ©es
amoxicillin script [url=https://amoxicillin.bid/#]amoxicillin online canada[/url] amoxicillin 500 mg tablet price
http://ivermectin.store/# stromectol 15 mg
buy prednisone tablets online [url=http://prednisonetablets.shop/#]prednisone 10mg cost[/url] how can i get prednisone online without a prescription
ivermectin 50ml [url=http://ivermectin.store/#]ivermectin 6mg dosage[/url] stromectol for humans
https://prednisonetablets.shop/# prednisone 20 mg tablet price
stromectol 3 mg tablets price [url=http://ivermectin.store/#]stromectol pill[/url] ivermectin humans
order tizanidine online cheap tizanidine online buy generic zanaflex over the counter
cheap clomid now [url=https://clomiphene.icu/#]can you buy generic clomid without a prescription[/url] where buy cheap clomid without insurance
zithromax online [url=https://azithromycin.bid/#]zithromax online usa no prescription[/url] where to buy zithromax in canada
http://prednisonetablets.shop/# prednisone over the counter south africa
buying from online mexican pharmacy [url=http://mexicanpharm.shop/#]Online Mexican pharmacy[/url] mexico pharmacies prescription drugs mexicanpharm.shop
deltasone 40mg pill purchase deltasone buy deltasone 10mg for sale
best online pharmacy india [url=https://indianpharm.store/#]international medicine delivery from india[/url] best india pharmacy indianpharm.store
https://indianpharm.store/# reputable indian online pharmacy indianpharm.store
online shopping pharmacy india [url=http://indianpharm.store/#]reputable indian pharmacies[/url] indian pharmacy online indianpharm.store
medication from mexico pharmacy [url=http://mexicanpharm.shop/#]Certified Pharmacy from Mexico[/url] mexican mail order pharmacies mexicanpharm.shop
http://mexicanpharm.shop/# mexico pharmacies prescription drugs mexicanpharm.shop
canadian neighbor pharmacy: Certified Online Pharmacy Canada – canadian pharmacy review canadianpharm.store
mexico drug stores pharmacies [url=http://mexicanpharm.shop/#]Online Pharmacies in Mexico[/url] reputable mexican pharmacies online mexicanpharm.shop
accutane for sale online buy accutane 20mg without prescription generic isotretinoin 40mg
https://canadianpharm.store/# best canadian pharmacy online canadianpharm.store
mexican pharmacy [url=https://mexicanpharm.shop/#]Certified Pharmacy from Mexico[/url] buying prescription drugs in mexico mexicanpharm.shop
Online medicine home delivery [url=http://indianpharm.store/#]Indian pharmacy to USA[/url] indian pharmacies safe indianpharm.store
pharmacies in mexico that ship to usa: mexican mail order pharmacies – mexican pharmaceuticals online mexicanpharm.shop
canadian pharmacy drugs online [url=http://canadianpharm.store/#]Pharmacies in Canada that ship to the US[/url] canadian pharmacy tampa canadianpharm.store
order albuterol inhalator generic buy generic albuterol albuterol cheap
thecanadianpharmacy [url=https://canadianpharm.store/#]Best Canadian online pharmacy[/url] canadian pharmacy ltd canadianpharm.store
mexican pharmacy [url=https://mexicanpharm.shop/#]Online Pharmacies in Mexico[/url] best online pharmacies in mexico mexicanpharm.shop
https://canadianpharm.store/# adderall canadian pharmacy canadianpharm.store
amoxicillin price where to buy amoxicillin without a prescription cheap amoxicillin without prescription
Every roll is a winner at Enso, but there’s so much more than just rolls. The freshest sushi, sashimi and traditional and innovative Japanese favorites await. A down home local’s casino, family owned and operated, the Wild Card Saloon and Casino on Main Street in Black Hawk is nestled next door to Bull Durham Casino across from the Mill City Chophouse. Black Gold Casino – The Black and Gold Casino is a small space casino spanning up to only 3,744 square feet of the gaming floor. However, it houses more than 200 of the best new electronic games. The ambiance of the place and the services provided by the staff makes up for its small size. You can also join the Wildcatters club and check out the benefits and chances that come with the membership. The distance from Dallas to Black and Gold Casino can be covered in 2 hours Address : 288 Mulberry Ln, Wilson, OK 73463 Timing : 8 am to 4 am Distance from Dallas : 117.9 miles
https://victor-wiki.win/index.php?title=Liberty_slots_free_spins_no_deposit
Here are some essential details you need to know about the ‘Holiday Spins Splash’ bonus program: 18+ | Regler och villkor gäller | Spela casino ansvarsfullt | Stodlinjen.se Endast nya medlemmar. Gäller på första insättningen på minst 100 kr. 200 bonusspins (50 öre spinn) gäller endast på Fire Joker, tillgängliga i 48 timmar. Vinster från bonusspins behöver omsättas 40x inom 60 dagar. Great! Successfully subscribed. Great! Successfully subscribed. Caxino Casino’s is a top paying online casino whose payout percentage sits somewhere between 95% and 97%. You can benefit from a payout percentage of up to 99% on tables games like blackjack. Caxino Casino is relatively new, yet they offer New Zealanders a decent catalogue of games, bonuses, and fair promotions. One of the advantages of playing at Caxino Casino is that the site is supported by award-winning casino software providers like NetEnt, Evolution and Microgaming.
top online pharmacies [url=http://canadadrugs.pro/#]canadian pharmacieswith no prescription[/url] most reliable canadian pharmacy
http://canadadrugs.pro/# canadian pharmacy online
canadian pharmacies [url=https://canadadrugs.pro/#]discount mail order pharmacy[/url] best canadian pharmacy for viagra
oral amoxiclav amoxiclav pill order augmentin 1000mg pills
canadian pharmacy drugstore [url=http://canadadrugs.pro/#]online prescriptions without script[/url] reputable canadian mail order pharmacy
overseas no rx drugs online [url=https://canadadrugs.pro/#]fda approved canadian pharmacies[/url] canada pharmacies top best
order levothyroxine without prescription buy synthroid 75mcg for sale order synthroid 75mcg pill
safe online pharmacies: online discount pharmacy – cheap canadian drugs
It’s easy and low-risk to buy cryptocurrency – in the amount that’s right for you CEX.IO supports multiple payment methods for purchasing cryptocurrencies. Whether you buy bitcoin with a credit card or via bank transfer, CEX.IO makes it easy and safe. It combines competitive fees, user-friendly navigation, and attractive prices to provide cost-effective trading conditions for users. Additionally, a straightforward process for making a purchase eliminates uncertainty. From how to set up a crypto wallet, documents to have, and making your first Bitcoin transaction, let Invity be your cryptocurrency guide. Bitcoin offers a decentralized, transparent, and secure monetary system, immune to inflation and political manipulation. With lower transaction fees, fast global transfers, and finite supply, it can be a superior alternative to traditional investments.
https://marcopyhf263815.frewwebs.com/24920519/manual-article-review-is-required-for-this-article
How does the market feel about Squid Game today? The SQUID token can be used only in the Squid Game project, an online game that’s set to start in November. (No lives, the gamemakers pledge, will be sacrificed as part of the game.) Players need to present a certain number to play or to restart the game if they fail. Entry fees range from 650 tokens to 15,000. Of those entry fees in games, 10% is sent to the token’s developers, with the rest making up the award pool for the winner of the game. On November 20, 2023, the U.S. Securities and Exchange Commission (SEC) filed a lawsuit against the cryptocurrency exchange Kraken. The SEC accused Kraken of operating an unregistered securities exchange and purportedly mixing customer funds with its own. As a result, crypto exchanges facilitating the trading of these tokens are obligated to undergo registration as securities exchanges.
buy omnacortil 40mg sale omnacortil 20mg ca buy prednisolone
prescription drugs without prior prescription [url=http://edwithoutdoctorprescription.pro/#]cialis without a doctor prescription canada[/url] buy prescription drugs online without
legitimate canadian online pharmacies [url=http://canadianinternationalpharmacy.pro/#]canada pharmacy 24h[/url] canadian pharmacies
canadian mail order pharmacy [url=http://canadianinternationalpharmacy.pro/#]best canadian pharmacy[/url] canadapharmacyonline legit
clomiphene 50mg cost buy clomid online order clomiphene 100mg pill
mexico drug stores pharmacies [url=https://certifiedpharmacymexico.pro/#]medication from mexico pharmacy[/url] pharmacies in mexico that ship to usa
mexican drugstore online [url=https://certifiedpharmacymexico.pro/#]mexico pharmacies prescription drugs[/url] medicine in mexico pharmacies
buy generic neurontin 100mg neurontin 800mg drug generic gabapentin 600mg
buy medicines online in india [url=http://medicinefromindia.store/#]reputable indian pharmacies[/url] indian pharmacies safe
mexico pharmacies prescription drugs [url=https://certifiedpharmacymexico.pro/#]mexican pharmacy[/url] pharmacies in mexico that ship to usa
prescription drugs [url=https://edwithoutdoctorprescription.pro/#]cheap cialis[/url] discount prescription drugs
medicine in mexico pharmacies [url=http://certifiedpharmacymexico.pro/#]buying prescription drugs in mexico online[/url] mexico pharmacies prescription drugs
buying prescription drugs in mexico [url=https://certifiedpharmacymexico.pro/#]mexico drug stores pharmacies[/url] medicine in mexico pharmacies
where can i buy lasix buy furosemide 40mg pill buy furosemide diuretic
sildenafil 50mg canada sildenafil 50mg tablets overnight viagra delivery
ed pills gnc [url=http://edpill.cheap/#]cheap erectile dysfunction pills[/url] male ed pills
india pharmacy [url=https://medicinefromindia.store/#]indian pharmacies safe[/url] mail order pharmacy india
http://medicinefromindia.store/# indian pharmacies safe
You can see from the information provided on this page the many benefits you get from signing up for a low minimum deposit sportsbook USA. You can clearly see how a $1 sports betting minimum deposit is something you should certainly be keeping an eye out for, especially if you are starting your betting experience on a budget. Multiple US sportsbooks and operators want to make their products as appealing as possible, and offering low deposits is one of the best ways they can do this. If you decide you want to try and enter the world of online sports betting for the first time, make sure you shop around between the various sites before committing. Betting markets, also known as betting lines, are a critical component of the online gambling experience. They provide variety, show a sportsbook’s expertise, and almost always feature competitive odds. Our top recommended low minimum deposit sports betting sites offer a wide range of betting lines on all major sports and events, including moneyline bets, totals, point spreads, props, futures, and more. This extensive selection of betting markets allows bettors to find the perfect bet for their style and preference.
https://garretthkhg074185.dsiblogger.com/52319898/online-cricket-betting-apps-india
North Geelong – Oakleigh Cannons Canberra Croatia – Tigers FC Hafnarfjordur – Vikingur Reykjavik Fram – Fylkir Charlestown Azzurri – Broadmeadow Angelholm – Eskilsminne Sutherland Sharks – Mount Druitt Rangers U. De Chile – O’Higgins Vestri – Selfoss Grotta – Akranes … We cover all your favorite teams, as well as highly obscure teams and picks. Picks cover all bet types, from moneyline to over under to against the spread to player props and fun parlay picks. The best part is simply that we provide free picks for many sports each and every day. There are many sites that free soccer betting tips and that includes Bookies. We have the best soccer bets today and every day, with selections available for leagues all over the world. We will highlight the best soccer betting sites where you can claim a signup bonus. Make sure that you follow a staking plan when betting.
cheap erectile dysfunction [url=http://edpill.cheap/#]best ed pill[/url] best ed drug
rybelsus ca semaglutide 14mg cheap order semaglutide 14 mg online cheap
order monodox online cheap vibra-tabs monodox ca
buying prescription drugs in mexico [url=http://certifiedpharmacymexico.pro/#]medication from mexico pharmacy[/url] mexican pharmaceuticals online
mexican border pharmacies shipping to usa [url=https://mexicanph.shop/#]best online pharmacies in mexico[/url] best online pharmacies in mexico
buying from online mexican pharmacy mexico pharmacies prescription drugs buying prescription drugs in mexico
mexican mail order pharmacies [url=https://mexicanph.com/#]mexican border pharmacies shipping to usa[/url] medication from mexico pharmacy
mexican drugstore online buying from online mexican pharmacy mexican border pharmacies shipping to usa
online casino real money usa casino slot games online casino usa
mexican border pharmacies shipping to usa buying prescription drugs in mexico online mexican border pharmacies shipping to usa
purple pharmacy mexico price list mexico pharmacies prescription drugs mexican pharmacy
pregabalin over the counter lyrica 150mg brand buy pregabalin without prescription
medicine in mexico pharmacies reputable mexican pharmacies online mexico pharmacy
hydroxychloroquine 400mg tablet hydroxychloroquine order hydroxychloroquine cost
mexico drug stores pharmacies purple pharmacy mexico price list mexico pharmacies prescription drugs
mexican drugstore online mexican drugstore online mexican pharmaceuticals online
best online pharmacies in mexico mexican mail order pharmacies reputable mexican pharmacies online
purple pharmacy mexico price list buying from online mexican pharmacy mexican online pharmacies prescription drugs
medication from mexico pharmacy buying prescription drugs in mexico online reputable mexican pharmacies online
order triamcinolone 10mg generic buy aristocort 4mg for sale buy aristocort pill
reputable mexican pharmacies online buying from online mexican pharmacy mexican pharmaceuticals online
mexican online pharmacies prescription drugs mexican pharmacy reputable mexican pharmacies online
purple pharmacy mexico price list mexican mail order pharmacies buying prescription drugs in mexico online
cialis mail order us cheap tadalafil pill tadalafil cialis
medication from mexico pharmacy mexico drug stores pharmacies mexico drug stores pharmacies
mexican rx online buying prescription drugs in mexico online medication from mexico pharmacy
buying prescription drugs in mexico mexican online pharmacies prescription drugs mexican online pharmacies prescription drugs
mexican border pharmacies shipping to usa mexico drug stores pharmacies mexican online pharmacies prescription drugs
mexican drugstore online best mexican online pharmacies best online pharmacies in mexico
You Have A Gift For Explaining Things In An Understandable Way. Thank You!
buying prescription drugs in mexico online mexico pharmacy best online pharmacies in mexico
mexican border pharmacies shipping to usa buying prescription drugs in mexico mexican rx online
mexican mail order pharmacies mexico drug stores pharmacies buying prescription drugs in mexico online
purple pharmacy mexico price list mexican border pharmacies shipping to usa pharmacies in mexico that ship to usa
Your blog is a true gift to the world. We’re big fans from Asheville!
medicine in mexico pharmacies buying from online mexican pharmacy buying prescription drugs in mexico online
desloratadine medication clarinex 5mg price clarinex over the counter
mexico pharmacy mexican pharmacy best online pharmacies in mexico
mexican online pharmacies prescription drugs mexican rx online mexican online pharmacies prescription drugs
medicine in mexico pharmacies mexican pharmacy mexican pharmaceuticals online
mexican pharmaceuticals online best mexican online pharmacies mexican drugstore online
best online pharmacies in mexico mexico drug stores pharmacies mexican rx online
https://mexicanph.com/# buying prescription drugs in mexico
pharmacies in mexico that ship to usa [url=https://mexicanph.shop/#]mexican rx online[/url] mexico drug stores pharmacies
Your blog is a true masterpiece, crafted with care and passion. We’re proud supporters from Asheville!
order cenforce 100mg generic cenforce drug order cenforce 100mg generic
mexican rx online mexico pharmacy mexico drug stores pharmacies
mexico drug stores pharmacies п»їbest mexican online pharmacies buying from online mexican pharmacy
http://mexicanph.shop/# п»їbest mexican online pharmacies
purple pharmacy mexico price list
Your blog is a true gem in the vast sea of the internet. Sending love and appreciation from Asheville!
mexican pharmaceuticals online mexican pharmacy purple pharmacy mexico price list
Your writing is like a gentle breeze, refreshing and uplifting. We’re big fans of your blog from Asheville!
medicine in mexico pharmacies mexico drug stores pharmacies mexico drug stores pharmacies
Your blog is like a breath of fresh air. In Asheville, we’re big fans and can’t wait for more!
Your blog is like a good friend – reliable, comforting, and always there when you need it. Sending love from Asheville!
mexican pharmacy mexican rx online mexican rx online
mexico drug stores pharmacies medicine in mexico pharmacies mexican drugstore online
mexico drug stores pharmacies buying from online mexican pharmacy medication from mexico pharmacy
Your blog is a true gift to the world. We’re big fans from Asheville!
http://mexicanph.shop/# mexican border pharmacies shipping to usa
purple pharmacy mexico price list [url=http://mexicanph.shop/#]buying from online mexican pharmacy[/url] mexico drug stores pharmacies
Your blog is a true gem in the vast sea of the internet. Sending love and appreciation from Asheville!
mexico drug stores pharmacies purple pharmacy mexico price list mexico pharmacies prescription drugs
medicine in mexico pharmacies best online pharmacies in mexico mexican pharmacy
buying prescription drugs in mexico reputable mexican pharmacies online mexico pharmacies prescription drugs
http://mexicanph.com/# mexican mail order pharmacies
reputable mexican pharmacies online
loratadine 10mg ca order claritin 10mg for sale claritin over the counter
mexico drug stores pharmacies mexico pharmacy mexican mail order pharmacies
Your posts always leave me feeling enlightened and inspired. Thank you for sharing your knowledge with us. Asheville sends its love!
Your writing has a way of touching hearts and minds. We’re proud supporters of your blog from Asheville!
mexican pharmacy mexican pharmacy pharmacies in mexico that ship to usa
buy aralen pills for sale buy aralen 250mg for sale chloroquine 250mg tablet
buying from online mexican pharmacy mexican rx online mexico drug stores pharmacies
amoxicillin 500mg buy online canada: where can i get amoxicillin 500 mg – amoxicillin medicine
http://lisinopril.top/# lisinopril 20 mg tablet price
amoxicillin buy no prescription: buy amoxicillin 500mg usa – amoxicillin 500 mg without a prescription
http://lisinopril.top/# buy prinivil online
https://buyprednisone.store/# steroids prednisone for sale
http://furosemide.guru/# furosemide 100mg
minocycline 100mg acne [url=https://stromectol.fun/#]where can i buy stromectol[/url] minocycline 50mg without prescription
stromectol price usa: stromectol tablets for humans for sale – where can i buy oral ivermectin
prednisone 20 mg: prednisone 20 mg in india – prednisone 10mg tablet price
https://furosemide.guru/# lasix medication
https://lisinopril.top/# lisinopril 5 mg tabs
prednisone steroids: prednisone 10 mg brand name – prednisone online paypal
https://stromectol.fun/# ivermectin 5 mg
https://buyprednisone.store/# order prednisone 10 mg tablet
Thank you for sharing your expertise with the world through your blog. Asheville residents are grateful for your contributions.
amoxicillin online purchase: amoxicillin for sale – amoxicillin online canada
Your blog is a treasure trove of information. Thank you for sharing your wisdom with us. Asheville can’t get enough!
how much is lisinopril 10 mg: lisinopril 5 mg uk price – buy zestoretic online
http://furosemide.guru/# lasix 100 mg
https://lisinopril.top/# lisinopril 20mg discount
20 mg of prednisone [url=http://buyprednisone.store/#]prednisone 12 tablets price[/url] can i buy prednisone online without prescription
metformin 500mg pills order glycomet 500mg pills metformin 500mg for sale
order prednisone: prednisone 20mg online – prednisone 10 mg canada
furosemida 40 mg [url=https://furosemide.guru/#]Buy Lasix[/url] lasix 20 mg
https://buyprednisone.store/# prednisone 50 mg buy
ivermectin 0.5: buy stromectol online – ivermectin tablets uk
lisinopril medication prescription: lisinopril prescription coupon – buying lisinopril in mexico
http://buyprednisone.store/# prednisone pills cost
http://stromectol.fun/# minocycline indications
order metformin 1000mg pills brand glucophage 500mg glycomet 500mg price
order lisinopril online us [url=http://lisinopril.top/#]lisinopril price comparison[/url] lisinopril buy online
lasix tablet: Buy Lasix – lasix generic
https://furosemide.guru/# furosemida
by prednisone w not prescription: where can i buy prednisone – prednisone buy canada
Your blog is a shining example of excellence in the online sphere. We’re proud supporters from Asheville!
http://amoxil.cheap/# where to buy amoxicillin 500mg
http://furosemide.guru/# lasix online
prednisone brand name [url=https://buyprednisone.store/#]prednisone 2.5 tablet[/url] buy prednisone online usa
https://amoxil.cheap/# amoxicillin for sale
lisinopril 20 mg cost: lisinopril 2mg tablet – lisinopril for sale online
buy generic orlistat online diltiazem oral diltiazem generic
http://stromectol.fun/# stromectol australia
What a fantastic article! We’re big fans of your blog here in Asheville and eagerly await your next post.
http://amoxil.cheap/# order amoxicillin online no prescription
Your blog is a true gem in the vast sea of the internet. Sending love and appreciation from Asheville!
where can i buy amoxocillin: where can i buy amoxicillin over the counter uk – amoxicillin 500mg price in canada
http://furosemide.guru/# furosemide 100mg
http://stromectol.fun/# ivermectin cost in usa
http://lisinopril.top/# lisinopril 250mg
minocycline 100mg tablets [url=https://stromectol.fun/#]stromectol covid[/url] buy minocycline online
buy cheap atorvastatin order atorvastatin 20mg pill atorvastatin 20mg us
https://amoxil.cheap/# buy amoxil
Your words have the power to uplift and inspire. Thank you for sharing your gift with us. Asheville loves your blog!
fast shipping prednisone: prednisone 20mg for sale – 40 mg prednisone pill
https://amoxil.cheap/# amoxicillin 500mg for sale uk
cost for 40 mg lisinopril: zestril 20 mg – lisinopril 5 mg canada
https://stromectol.fun/# stromectol tab
https://buyprednisone.store/# cost of prednisone in canada
ivermectin lotion price: buy stromectol uk – stromectol medication
Your blog posts are always a joy to read! From Asheville with love, we appreciate your work.
http://stromectol.fun/# stromectol brand
https://stromectol.fun/# ivermectin lotion cost
https://stromectol.fun/# ivermectin 18mg
what is minocycline prescribed for [url=http://stromectol.fun/#]ivermectin 2mg[/url] minocycline 50mg pills
Your blog is like a ray of sunshine on a cloudy day – uplifting and inspiring. Sending love from Asheville!
over the counter prednisone medicine: prednisone 10 mg – order prednisone online canada
norvasc where to buy order generic norvasc 10mg how to get norvasc without a prescription
https://furosemide.guru/# furosemide 100mg
lasix 100 mg: Buy Furosemide – lasix 40 mg
http://furosemide.guru/# lasix online
http://lisinopril.top/# lisinopril 5 mg tablet
generic ivermectin: ivermectin 50mg/ml – where can i buy oral ivermectin
acyclovir 400mg uk buy zovirax 800mg generic allopurinol online
http://amoxil.cheap/# 875 mg amoxicillin cost
http://furosemide.guru/# lasix uses
prednisone 60 mg tablet: prednisone 1 mg tablet – can you buy prednisone over the counter in canada
http://stromectol.fun/# stromectol 3 mg price
buy amoxicillin online with paypal [url=https://amoxil.cheap/#]how to buy amoxycillin[/url] where to buy amoxicillin
http://buyprednisone.store/# 5mg prednisone
lisinopril 3: cheapest lisinopril 10 mg – lisinopril pills for sale
http://stromectol.fun/# ivermectin 8000
http://buyprednisone.store/# prednisone 5mg cost
lasix pills: lasix 40mg – furosemide 40 mg
http://lisinopril.top/# prinivil 20mg tabs
order prinivil zestril 2.5mg brand zestril pill
http://stromectol.fun/# ivermectin 1 cream
amoxicillin 500mg buy online uk: amoxicillin 500 tablet – amoxicillin 200 mg tablet
https://furosemide.guru/# lasix 40mg
http://buyprednisone.store/# where can you buy prednisone
10mg generic 10mg lisinopril [url=https://lisinopril.top/#]lisinopril 80[/url] generic zestoretic
order crestor 20mg pill order generic ezetimibe 10mg buy zetia 10mg pill
Thank you for consistently delivering top-notch content. We’re huge fans of your blog here in Asheville!
http://amoxil.cheap/# amoxicillin 500mg price canada
prinivil 5mg tablet: lisinopril 10 12.5 mg tablets – 16 lisinopril
http://stromectol.fun/# stromectol cost
amoxicillin capsule 500mg price: how to get amoxicillin – generic amoxicillin
http://amoxil.cheap/# where can i get amoxicillin
order prilosec 20mg without prescription order generic omeprazole 10mg omeprazole 20mg oral
domperidone sale motilium over the counter buy generic tetracycline
top 10 pharmacies in india india pharmacy mail order indian pharmacy online
http://indianph.xyz/# online shopping pharmacy india
http://indianph.xyz/# top 10 online pharmacy in india
buy medicines online in india
https://indianph.xyz/# reputable indian pharmacies
best india pharmacy
https://indianph.xyz/# buy medicines online in india
mail order pharmacy india
reputable indian pharmacies pharmacy website india india pharmacy mail order
https://indianph.xyz/# reputable indian pharmacies
indian pharmacy online
http://indianph.com/# indianpharmacy com
best india pharmacy
https://indianph.xyz/# top online pharmacy india
https://indianph.xyz/# pharmacy website india
india pharmacy
oral lopressor 100mg buy lopressor 100mg online cheap buy metoprolol 50mg pill
https://indianph.com/# top online pharmacy india
legitimate online pharmacies india
indian pharmacies safe best online pharmacy india buy medicines online in india
https://indianph.xyz/# buy medicines online in india
legitimate online pharmacies india
order flexeril 15mg for sale flexeril drug ozobax drug
https://indianph.com/# india pharmacy
indian pharmacies safe
https://doxycycline.auction/# doxycycline 100mg capsules
tamoxifen hot flashes: liquid tamoxifen – tamoxifen buy
https://nolvadex.guru/# nolvadex side effects
tenormin 50mg over the counter tenormin for sale generic atenolol
buy doxycycline: order doxycycline 100mg without prescription – doxycycline prices
https://doxycycline.auction/# buy doxycycline without prescription
toradol online buy colcrys cheap colchicine ca
https://cipro.guru/# buy cipro online canada
diflucan otc australia: where to buy diflucan in uk – best diflucan price
https://cytotec24.com/# Cytotec 200mcg price
https://doxycycline.auction/# doxycycline hyc
diflucan cap 150 mg: can you buy diflucan over the counter in mexico – diflucan for sale uk
eva elfie video: eva elfie izle – eva elfie filmleri
Angela White video: Abella Danger – abella danger izle
lana rhoades: lana rhoades – lana rhodes
Angela Beyaz modeli: abella danger izle – abella danger izle
eva elfie: eva elfie video – eva elfie filmleri
https://angelawhite.pro/# Angela White filmleri
?????? ????: Angela White – ?????? ????
http://abelladanger.online/# Abella Danger
http://sweetiefox.online/# sweeti fox
Angela White: abella danger video – abella danger filmleri
http://lanarhoades.fun/# lana rhoades
Sweetie Fox modeli: Sweetie Fox izle – swetie fox
http://lanarhoades.fun/# lana rhoades
http://evaelfie.pro/# eva elfie izle
lana rhoades video: lana rhodes – lana rhoades izle
http://sweetiefox.online/# Sweetie Fox video
?????? ????: ?????? ???? – Angela White video
https://abelladanger.online/# abella danger izle
lana rhoades video: lana rhoades modeli – lana rhodes
lana rhoades boyfriend: lana rhoades – lana rhoades pics
https://evaelfie.site/# eva elfie new video
https://sweetiefox.pro/# sweetie fox full
mia malkova movie: mia malkova – mia malkova photos
https://lanarhoades.pro/# lana rhoades hot
ph sweetie fox: sweetie fox new – ph sweetie fox
http://lanarhoades.pro/# lana rhoades pics
lana rhoades unleashed: lana rhoades boyfriend – lana rhoades solo
lana rhoades pics: lana rhoades pics – lana rhoades hot
http://sweetiefox.pro/# sweetie fox video
eva elfie hot: eva elfie – eva elfie hot
https://sweetiefox.pro/# ph sweetie fox
lana rhoades hot: lana rhoades hot – lana rhoades hot
http://miamalkova.life/# mia malkova girl
lana rhoades: lana rhoades hot – lana rhoades hot
https://miamalkova.life/# mia malkova
sweetie fox full: sweetie fox cosplay – fox sweetie
lana rhoades boyfriend: lana rhoades unleashed – lana rhoades full video
http://sweetiefox.pro/# sweetie fox full video
sweetie fox new: sweetie fox video – sweetie fox
mia malkova videos: mia malkova new video – mia malkova new video
http://sweetiefox.pro/# ph sweetie fox
eva elfie: eva elfie – eva elfie new video
eva elfie new videos: eva elfie – eva elfie photo
http://evaelfie.site/# eva elfie
eva elfie full videos: eva elfie full video – eva elfie
https://sweetiefox.pro/# ph sweetie fox
aviator oyunu: aviator oyna slot – pin up aviator
jogar aviator Brasil: aviator pin up – aviator jogo
http://aviatoroyunu.pro/# aviator bahis
aviator oficial pin up: aviator oficial pin up – pin-up
https://aviatormalawi.online/# aviator bet
pin up aviator: pin up cassino online – pin-up casino entrar
http://aviatormalawi.online/# aviator game
aviator oyunu: aviator hilesi – aviator sinyal hilesi
aviator jogar: aviator bet – jogar aviator Brasil
jogar aviator online: jogar aviator Brasil – pin up aviator
pin-up casino login: pin up cassino online – aviator pin up casino
melhor jogo de aposta para ganhar dinheiro: jogos que dão dinheiro – site de apostas
aviator game: aviator malawi – play aviator
aviator game: aviator bet – aviator jogar
depósito mínimo 1 real: melhor jogo de aposta para ganhar dinheiro – aplicativo de aposta
zithromax capsules: zithromax capsules price – zithromax 250 mg
pin up cassino online: pin-up cassino – pin up aviator
aviator jogo de aposta: jogo de aposta online – jogo de aposta online
buy zithromax 1000mg online: zithromax for sale usa – buy zithromax
pin up aviator: jogar aviator Brasil – aviator game
zithromax purchase online: generic zithromax india – zithromax for sale 500 mg
india online pharmacy: Best Indian pharmacy – reputable indian online pharmacy indianpharm.store
The opinions above encapsulate my thoughts – this post is a masterpiece!
canadian pharmacy no scripts: Cheapest drug prices Canada – safe canadian pharmacy canadianpharm.store
http://canadianpharmlk.com/# canadian pharmacy online canadianpharm.store
buying prescription drugs in mexico online: Medicines Mexico – buying from online mexican pharmacy mexicanpharm.shop
http://canadianpharmlk.shop/# canadian pharmacy no scripts canadianpharm.store
https://indianpharm24.com/# indian pharmacy paypal indianpharm.store
https://indianpharm24.shop/# online shopping pharmacy india indianpharm.store
77 canadian pharmacy: Certified Canadian pharmacies – canada rx pharmacy canadianpharm.store
http://mexicanpharm24.com/# mexico pharmacies prescription drugs mexicanpharm.shop
https://mexicanpharm24.shop/# buying prescription drugs in mexico mexicanpharm.shop
http://indianpharm24.com/# buy prescription drugs from india indianpharm.store
mexico pharmacy: Medicines Mexico – mexico drug stores pharmacies mexicanpharm.shop
http://indianpharm24.shop/# buy medicines online in india indianpharm.store
https://canadianpharmlk.com/# canadian family pharmacy canadianpharm.store
https://indianpharm24.com/# buy prescription drugs from india indianpharm.store
http://canadianpharmlk.shop/# canadian pharmacies that deliver to the us canadianpharm.store
http://canadianpharmlk.com/# canadian pharmacy review canadianpharm.store
how to get generic clomid pills: taking clomid and testosterone together – how can i get generic clomid without dr prescription
http://amoxilst.pro/# generic amoxicillin
http://amoxilst.pro/# amoxicillin 500mg capsules antibiotic
prednisone 20mg capsule: what is prednisone used for in adults – prednisone 5 mg tablet
https://clomidst.pro/# can you get generic clomid without dr prescription
http://prednisonest.pro/# can you buy prednisone over the counter in usa
https://amoxilst.pro/# cost of amoxicillin prescription
https://clomidst.pro/# can you get clomid pills
http://onlinepharmacy.cheap/# cheapest pharmacy to get prescriptions filled
https://edpills.guru/# ed medication online
https://pharmnoprescription.pro/# prescription online canada
https://edpills.guru/# low cost ed meds online
http://edpills.guru/# low cost ed meds online
http://canadianpharm.guru/# maple leaf pharmacy in canada
http://pharmacynoprescription.pro/# no prescription online pharmacy
https://mexicanpharm.online/# buying prescription drugs in mexico
http://mexicanpharm.online/# mexican rx online
https://pharmacynoprescription.pro/# pharmacy no prescription required
https://indianpharm.shop/# buy medicines online in india
extraordinary morning starting with an excellent reading 🌞📰
http://pharmacynoprescription.pro/# quality prescription drugs canada
remarkable sunrise beginning with a fantastic reading 📚🌄
http://mexicanpharm.online/# mexican online pharmacies prescription drugs
https://canadianpharm.guru/# adderall canadian pharmacy
http://pharmacynoprescription.pro/# how to get prescription drugs from canada
https://indianpharm.shop/# reputable indian pharmacies
http://canadianpharm.guru/# cross border pharmacy canada
http://mexicanpharm.online/# mexico pharmacies prescription drugs
http://indianpharm.shop/# indian pharmacies safe
http://indianpharm.shop/# top 10 online pharmacy in india
gates of olympus demo turkce oyna: gates of olympus nas?l para kazanilir – gates of olympus
gates of olympus slot: gates of olympus demo turkce – gate of olympus hile
en guvenilir slot siteleri: slot siteleri – yeni slot siteleri
gates of olympus demo oyna: gates of olympus max win – gates of olympus oyna
gates of olympus slot: gates of olympus giris – pragmatic play gates of olympus
aviator oyunu 20 tl: ucak oyunu bahis aviator – aviator sinyal hilesi ucretsiz
pin up casino giris: pin up casino guncel giris – aviator pin up
pin-up giris: pin up 7/24 giris – pin up
pin-up casino indir: pin up casino giris – pin up casino guncel giris
sweet bonanza slot: sweet bonanza mostbet – sweet bonanza siteleri
https://sweetbonanza.bid/# sweet bonanza yasal site
http://sweetbonanza.bid/# sweet bonanza slot
reputable mexican pharmacies online: mexico pharmacy – medication from mexico pharmacy
reputable indian online pharmacy: Generic Medicine India to USA – buy medicines online in india
pharmacies in mexico that ship to usa: mexico pharmacy – buying from online mexican pharmacy
medication from mexico pharmacy: cheapest mexico drugs – mexico drug stores pharmacies
mexico pharmacies prescription drugs: mexico pharmacy – buying from online mexican pharmacy
online pharmacy india: Cheapest online pharmacy – best india pharmacy
india pharmacy: Generic Medicine India to USA – reputable indian online pharmacy
mexican online pharmacies prescription drugs: Mexican Pharmacy Online – mexico pharmacies prescription drugs
http://kamagraiq.shop/# Kamagra 100mg price
https://kamagraiq.com/# Kamagra 100mg price
https://kamagraiq.shop/# Kamagra 100mg price
https://tadalafiliq.com/# Cialis 20mg price in USA
https://kamagraiq.shop/# cheap kamagra
http://tadalafiliq.shop/# Cialis 20mg price
cialis for sale: cialis without a doctor prescription – buy cialis pill
https://kamagraiq.com/# cheap kamagra
http://mexicanpharmgrx.com/# mexico pharmacy
http://indianpharmgrx.shop/# best online pharmacy india
http://mexicanpharmgrx.shop/# purple pharmacy mexico price list
http://indianpharmgrx.com/# top 10 pharmacies in india
http://indianpharmgrx.com/# online shopping pharmacy india
http://indianpharmgrx.shop/# reputable indian pharmacies
https://canadianpharmgrx.com/# canadian pharmacy cheap
http://indianpharmgrx.shop/# top 10 pharmacies in india
https://canadianpharmgrx.com/# 77 canadian pharmacy
http://indianpharmgrx.shop/# legitimate online pharmacies india
http://canadianpharmgrx.com/# onlinecanadianpharmacy
https://canadianpharmgrx.com/# canadian pharmacy tampa
https://canadianpharmgrx.com/# canadian 24 hour pharmacy
https://mexicanpharmgrx.com/# buying from online mexican pharmacy
ciprofloxacin order online: where can i buy cipro online – ciprofloxacin 500 mg tablet price
ciprofloxacin mail online: cipro 500mg best prices – ciprofloxacin 500mg buy online
buy doxycycline online without prescription: where to get doxycycline – buy cheap doxycycline online
price of doxycycline: 200 mg doxycycline – doxycycline hyclate 100 mg cap
doxycycline without a prescription: buy doxycycline 100mg – buy doxycycline monohydrate
nolvadex for sale: tamoxifen and weight loss – nolvadex pills
cost of diflucan over the counter: diflucan no prescription – diflucan otc where to buy
generic diflucan: diflucan 150 mg pill – where can i buy over the counter diflucan
nolvadex steroids: nolvadex price – nolvadex vs clomid
buy diflucan online india: diflucan 150 mg – diflucan 50 mg capsule
femara vs tamoxifen: nolvadex for sale amazon – tamoxifen for gynecomastia reviews
Abortion pills online: buy cytotec in usa – cytotec pills online
cipro ciprofloxacin: ciprofloxacin over the counter – buy ciprofloxacin over the counter
buy cipro: cipro pharmacy – ciprofloxacin 500mg buy online
diflucan over the counter south africa: diflucan cap 150 mg – diflucan 150
amoxicillin price without insurance: amoxicillin 825 mg – can we buy amoxcillin 500mg on ebay without prescription
buy zithromax: zithromax coupon – can i buy zithromax over the counter
zithromax for sale 500 mg: generic zithromax over the counter – cost of generic zithromax
stromectol tablets 3 mg: ivermectin ireland – buy ivermectin cream
purchase prednisone no prescription: prednisone 10mg tablet price – prednisone purchase canada
prednisone 20 mg prices: prednisone over the counter – buy prednisone online without a script
how to buy generic clomid without prescription: can i order generic clomid – cost of clomid pill
prednisone over the counter: prednisone nz – 5mg prednisone
https://medicationnoprescription.pro/# online drugs no prescription
https://onlinepharmacyworld.shop/# canada drugs coupon code
https://edpill.top/# ed online meds
https://medicationnoprescription.pro/# canadian and international prescription service
https://onlinepharmacyworld.shop/# cheapest pharmacy for prescriptions
http://medicationnoprescription.pro/# purchasing prescription drugs online
https://medicationnoprescription.pro/# order medication without prescription
https://edpill.top/# low cost ed meds
http://edpill.top/# best online ed treatment
https://medicationnoprescription.pro/# online pharmacy reviews no prescription
https://medicationnoprescription.pro/# no prescription online pharmacies
casino tr?c tuy?n: dánh bài tr?c tuy?n – casino tr?c tuy?n uy tín
casino tr?c tuy?n uy tín: game c? b?c online uy tín – casino tr?c tuy?n vi?t nam
https://casinvietnam.com/# casino tr?c tuy?n uy tin
casino online uy tín: casino online uy tín – web c? b?c online uy tín
choi casino tr?c tuy?n trên di?n tho?i: casino tr?c tuy?n uy tín – dánh bài tr?c tuy?n
Both airlines experienced better performance during the pandemic. Get breaking news and daily headlines delivered to your email inbox by signing up here. More on Payment Dallas Fort Worth International Airport (DFW) has been selected for the 2022 Airport Service Quality (ASQ) award for Best Airport that serves over 40 million passengers in North America by Airports Council International (ACI). Welcome to flightglobal. This website uses cookies to improve your experience and for ads personalisation. By continuing to browse this site you are agreeing to our use of these cookies. You can learn more about the cookies we use here. American announces plans for McDonnell Douglas MD-80 (also known as the Super 80) to join fleet in 1983. Click here to view This browser does not support the video element.
https://gregoryvtro396396.mybloglicious.com/42471241/top-100-online-bonus
Last updated Tuesday, March 21, 2023, at 1:28 PM. If you have any stories ideas feel free to shoot her a message at ariel.mallory@fox10tv Do you have a comment or question? Please let us know about it by sending us an email. Ryan is from the Atlanta area and graduated from Roswell High School in 2008. After graduation, he attended the University of South Alabama to pursue a degree in meteorology. His senior year, he was awarded the top forecaster award for the class of 2012. Albany, GA 31705 *You need to receive these channels in your TV channel line-up in order to watch them on the FOX Sports App. Some channels may not yet be available for every TV provider or on every platform. REMINDER: The Statewide Tornado Drill is scheduled for 9:50am Wednesday. This week is Severe Weather Awareness Week in Ohio. We all are encouraged to review our weather-related safety plans.
casino tr?c tuy?n vi?t nam: game c? b?c online uy tín – choi casino tr?c tuy?n trên di?n tho?i
casino tr?c tuy?n: web c? b?c online uy tín – dánh bài tr?c tuy?n
game c? b?c online uy tín: casino online uy tín – web c? b?c online uy tín
choi casino tr?c tuy?n trên di?n tho?i: casino tr?c tuy?n – casino online uy tín
choi casino tr?c tuy?n trên di?n tho?i: casino tr?c tuy?n vi?t nam – casino tr?c tuy?n vi?t nam
choi casino tr?c tuy?n trên di?n tho?i: casino tr?c tuy?n vi?t nam – casino tr?c tuy?n uy tín
https://indiaph24.store/# india pharmacy mail order
http://canadaph24.pro/# canadianpharmacyworld com
Be a Winner! Play the Best Online Casino Games Now! Casino PH
SightCare formula aims to maintain 20/20 vision without the need for any surgical process. This supplement is a perfect solution for people facing issues as they grow older. https://sightcare-web.com/
WeJiJ is here to help get you the best gaming setup, gaming PC and guide you through the games you like to play with news, reviews and guides. https://wejij.com/
Find the latest technology news and expert tech product reviews. Learn about the latest gadgets and consumer tech products for entertainment, gaming, lifestyle and more. https://axget.com/
Easier WWW is a leading technology site that is dedicated to produce great how-to, tips and tricks and cool software review. https://easierwww.com/
KeraBiotics is a meticulously-crafted natural formula designed to help people dealing with nail fungus. This solution, inspired by a sacred Amazonian barefoot tribe ritual https://kerabiotics-web.com/
Nagano Lean Body Tonic is a groundbreaking powdered supplement crafted to support your weight loss journey effortlessly. https://naganotonic-try.com/
– Shoot MASSIVE Loads For An Amazing Finish! https://semenax-try.com/
ZenCortex Research’s contains only the natural ingredients that are effective in supporting incredible hearing naturally.A unique team of health and industry professionals dedicated to unlocking the secrets of happier living through a healthier body. https://zencortex-try.com/
Tonic Greens is a ready-made greens shake designed to support the entire body and wellness of the mind. It is filled with over 50 individual vitamins https://tonicgreens-try.com/
MenoPhix is a menopause relief supplement featuring a blend of plant extracts to target the root cause of menopause symptoms. https://menophix-web.com/
Support the health of your ears with 100% natural ingredients, finally being able to enjoy your favorite songs and movies https://quietumplus-try.com/
Necessary cookies help make a website usable by enabling basic functions like page navigation and access to secure areas of the website. The website cannot function properly without these cookies. You can email the site owner to let them know you were blocked. Please include what you were doing when this page came up and the Cloudflare Ray ID found at the bottom of this page. Wondering what sets our predictions apart? We don’t just provide tips; we also explain the strategic reasons behind the decisions we make. Each suggestion is backed by a meticulous analysis of team dynamics, player form, recent performances, and external factors that could influence the outcome that produce hot prediction. So, what can you use your football predictions for? Well, there is a comprehensive range of betting markets on which you can take advantage of your predictions and tips. The most common markets that people tend to predict are match winners (in other words, predicting which side is going to win a specific game). However, there are many more bet types to look into.
https://eduardomnnn207483.blogginaway.com/26801291/babu88-wiki-bangladesh
All roads in the MLB lead to the World Series, with the winners of the American League and National League respectively clashing over a number of games to determine the overall champion. The games tend to be played on consecutive days, with the first two clashes taking place at the same ground before it’s switched to the opposing stadium for the next three ties. There are lots of teams who are competing to reach the MLB playoffs and World Series and it’s intriguing to find the teams who are going to fulfil their potential and end up at the business end of the competition. Our free MLB betting tips will give you an idea of the best Major League Baseball picks to make on a week-to-week basis, with the experts able to outline what sort of game we might expect as we go through the coupon.
FlowForce Max is an innovative, natural and effective way to address your prostate problems, while addressing your energy, libido, and vitality. https://flowforcemax-web.com/
CLINICALLY PROVEN* To Increase Semen Volume And Intensity https://semenax-try.com/
BioFit is a Nutritional Supplement That Uses Probiotics To Help You Lose Weight https://biofit-web.com/
Dentitox Pro is a liquid dietary solution created as a serum to support healthy gums and teeth. Dentitox Pro formula is made in the best natural way with unique, powerful botanical ingredients that can support healthy teeth. https://dentitox-us.com/
PureLumin Essence is a meticulously-crafted natural formula designed to help women improve the appearance of age spots. https://pureluminessence-web.com/
Alpha Tonic is a powder-based supplement that uses multiple natural herbs and essential vitamins and minerals to help optimize your body’s natural testosterone levels. https://alphatonic-web.com
VivoTonic™ is a 11-in-1 vital blood sugar support formula that may improve how the metabolism goes after the calories that consumers eat. https://vivotonic-web.com/
Progenifix is designed to help maximize weight loss results using a mixture of natural, science-backed ingredients. The formula also has secondary benefits, including promoting overall wellness and vitality and assisting your immune system. https://progenifix-web.com/
AquaPeace is an all-natural nutritional formula that uses a proprietary and potent blend of ingredients and nutrients to improve overall ear and hearing health and alleviate the symptoms of tinnitus. https://aquapeace-web.com
Fast Lean Pro is a herbal supplement that tricks your brain into imagining that you’re fasting and helps you maintain a healthy weight no matter when or what you eat. It offers a novel approach to reducing fat accumulation and promoting long-term weight management. https://fastleanpro-web.com/
100% Natural Formula Expressly Designed to Help Control Blood Sugar Levels, Improve Insulin Response And Support Overall Health https://glucotrusttry.com/
PowerBite stands as an innovative dental candy, dedicated to nurturing healthy teeth and gums. Infused with a potent formula, it champions the cause of a robust and radiant smile. Crafted meticulously https://powerbite-web.com/
Protoflow is a prostate health supplement featuring a blend of plant extracts, vitamins, minerals, fruit extracts, and more. https://protoflow-web.com/
Boostaro is a dietary supplement designed specifically for men who suffer from health issues. https://boostaro-try.com/
Zoracel is an extraordinary oral care product designed to promote healthy teeth and gums, provide long-lasting fresh breath, support immune health, and care for the ear, nose, and throat. https://zoracel-web.com
Cerebrozen is an excellent liquid ear health supplement purported to relieve tinnitus and improve mental sharpness, among other benefits. The Cerebrozen supplement is made from a combination of natural ingredients, and customers say they have seen results in their hearing, focus, and memory after taking one or two droppers of the liquid solution daily for a week. https://cerebrozen-try.com/
Zeneara is marketed as an expert-formulated health supplement that can improve hearing and alleviate tinnitus, among other hearing issues. https://zeneara-web.com/
GlucoBerry is one of the biggest all-natural dietary and biggest scientific breakthrough formulas ever in the health industry today. This is all because of its amazing high-quality cutting-edge formula that helps treat high blood sugar levels very naturally and effectively. https://glucoberry-web.com/
Pineal XT is a revolutionary supplement that promotes proper pineal gland function and energy levels to support healthy body function. https://pinealxt-web.com/
Carbofix is the revolutionary dietary formula that promises to activate weight loss without all the extra hard work. https://carbofix-try.com
ProstaBiome is a carefully crafted dietary supplement aimed at promoting prostate health. Bid farewell to restless nights and discomfort with ProstaBiome precise strategy for addressing prostate concerns. https://prostabiome-web.com/
PotentStream is designed to address prostate health by targeting the toxic, hard water minerals that can create a dangerous buildup inside your urinary system It’s the only dropper that contains nine powerful natural ingredients that work in perfect synergy to keep your prostate healthy and mineral-free well into old age. https://potentstream-web.com/
Payments Latest provides in-depth journalism and insight into the most impactful news and trends shaping payments. https://paymentslatest.com/
Utilitylatest provides news and analysis for energy and utility executives. We cover topics like smart grid tech, clean energy, regulation, generation, demand response, solar, storage, transmission distribution, and more. https://utilitylatest.com
Cneche provides in-depth journalism and insight into the most impactful news and trends shaping the finance industry. https://cneche.com/
Lasixiv provides news and analysis for IT executives. We cover big data, IT strategy, cloud computing, security, mobile technology, infrastructure, software and more. https://lasixiv.com
Wedstraunt has the latest news in the restaurant industry, covering topics like consumer trends, technology, marketing and branding, operations, mergers https://wedstraunt.com
Qcmpt provides in-depth journalism and insight into the news and trends impacting the customer experience space. https://qcmpt.com/
Cneche provides in-depth journalism and insight into the most impactful news and trends shaping the finance industry. https://cneche.com/
Tvphc provides news and analysis for IT executives. We cover big data, IT strategy, cloud computing, security, mobile technology, infrastructure, software and more. https://tvphc.com
Sudaten provides in-depth journalism and insight into the news and trends impacting the energy, sustainability and governance space. https://sudaten.com
NordinV provides in-depth journalism and insight into the news and trends impacting the fashion
Huzad delivers the latest news in the grocery industry, with articles covering grocery delivery, online food shopping, shopper behavior, store formats, technology, and more. https://huzad.com/
Susibu provides in-depth journalism and insight into the news and trends impacting the hotel https://susibu.com/
iwinpak provides in-depth journalism and insight into the news and trends impacting the manufacturing sector https://iwinpak.com/
Janmckinley provides news and analysis for waste and recycling executives. We cover topics like landfills, collections, regulation, waste-to-energy, corporate news, fleet management, and more. https://janmckinley.com
Sugar Defender is the rated blood sugar formula with an advanced blend of 24 proven ingredients that support healthy glucose levels and natural weight loss. https://mimsbrook.com
Sugar Defender is the rated blood sugar formula with an advanced blend of 24 proven ingredients that support healthy glucose levels and natural weight loss. https://mariscosleomar.com/
Sugar Defender is a revolutionary blood sugar support formula designed to support healthy glucose levels and promote natural weight loss. https://blackboxvending.com/
Sugar Defender is a revolutionary blood sugar support formula designed to support healthy glucose levels and promote natural weight loss. https://mineryuta.com
sugar defender: https://novabeaute.com/
sugar defender: https://abmdds.com/
sugar defender: https://peyfon.com/
sugar defender: https://nilayoram.com/
sugar defender: https://seahorsesoap.com/
sugar defender: https://sourceprousa.com/
sugar defender: https://flamebustersofkansas.com/
sugar defender: https://luckysloader.com/
sugar defender: https://lindadicesare.com/
sugar defender: https://alchemyfashiongroup.com/
sugar defender: https://bridgerealtysc.com/
The passion isn’t just inspiring—it’s downright seductive. Who knew a subject could be this enticing?
The finesse with which you articulated The points has me captivated. It’s as if you’re speaking my language.
The insights are like a sunrise, bringing light and warmth to new ideas.
The take on hard to understand topics is like a smooth ride in a luxury car—comfortable, yet exhilarating.
Refreshing take on the subject, like a cold splash of water to my long-held beliefs.
Thank you for visiting Libertatem, a dynamic online platform dedicated to the exploration and dissemination of legal knowledge, opinions, insights, and thought leadership. We are a vibrant community of legal professionals, law firms, law students, and anyone passionate about the world of law. Our mission is to foster a robust environment where legal minds come together to share, discuss, and advance the understanding of the ever-evolving legal landscape. For those who play correctly and you can comprehend the program from online game, then there’s all of the possibility to secure. The fresh Babu88 member system even lets professionals make much more. Still, playing has been current in the area for quite some time, that have owners getting wagers for the some activities. Yet not, people in Bangladesh had been entering betting websites because the growth of online gambling web sites. ABaby deal a multitude of antique infant things, including cribs, cradles, bassinets, strollers, and you will beddings.
https://arthurcsli336893.blogdal.com/27003325/manual-article-review-is-required-for-this-article
When it comes to Interface and Navigation, the Babu88 Bangladesh Official Website excels in providing a seamless and user-friendly experience. Our intuitive menu structure and clear categorization make it easy for you to locate your desired betting markets or access essential information with just a few clicks. Moreover, we have designed our website with accessibility in mind, ensuring compatibility with a range of devices, screen sizes, and browsers. This attention to detail guarantees that you can effortlessly navigate our platform and place bets without encountering any technical issues. Oops! You have landed to the 404 page but fortunately you can play the game or visit the popular page We’d like to highlight that from time to time, we may miss a potentially malicious software program. To continue promising you a malware-free catalog of programs and apps, our team has integrated a Report Software feature in every catalog page that loops your feedback back to us.
https://u.to/ghm3IA
https://gsean.lvziku.cn/home.php?mod=space&uid=433091
https://www.metooo.co.uk/u/665bd7b60c59a922425c1430
https://forumpoint.org/member.php?action=profile&uid=268310
The post has broadened my perspective in ways I didn’t expect. Thank you for that.
Such a well-researched piece! It’s evident how much effort you’ve put in.
Appreciate the balance and fairness, like a judge, but without the gavel.
Thoroughly insightful read, or so I thought until I realized it was The expertise shining through. Thanks for making me feel like a novice again!
nagano tonic: nagano tonic
Step into a world of endless fun—play online games now Lodibet
sugar defender rviews: https://sugardefenderreviews.pages.dev
sugar defender rviews: https://sugardefenderreviews.pages.dev
sugar defender rviews: https://sugardefenderreviews.pages.dev
sugar defender rviews: https://sugardefenderreviews.pages.dev
gluco6 rviews: https://gluco6reviews.usaloves.com/
Endless rewards and excitement await are you ready? Hawkplay
Vibrómetro
Sistemas de calibración: esencial para el operación suave y eficiente de las máquinas.
En el ámbito de la tecnología actual, donde la rendimiento y la fiabilidad del aparato son de suma trascendencia, los equipos de equilibrado tienen un tarea fundamental. Estos dispositivos adaptados están diseñados para ajustar y asegurar partes móviles, ya sea en herramientas de fábrica, medios de transporte de movilidad o incluso en equipos de uso diario.
Para los expertos en conservación de sistemas y los técnicos, operar con aparatos de ajuste es importante para garantizar el desempeño estable y estable de cualquier dispositivo giratorio. Gracias a estas opciones tecnológicas sofisticadas, es posible minimizar significativamente las oscilaciones, el ruido y la carga sobre los rodamientos, extendiendo la vida útil de elementos valiosos.
De igual manera importante es el tarea que tienen los equipos de ajuste en la servicio al usuario. El apoyo especializado y el mantenimiento constante utilizando estos equipos habilitan proporcionar prestaciones de óptima nivel, aumentando la bienestar de los usuarios.
Para los propietarios de negocios, la contribución en sistemas de ajuste y dispositivos puede ser esencial para incrementar la rendimiento y desempeño de sus dispositivos. Esto es especialmente significativo para los inversores que administran reducidas y pequeñas empresas, donde cada punto cuenta.
Además, los sistemas de calibración tienen una vasta utilización en el ámbito de la fiabilidad y el monitoreo de estándar. Facilitan identificar potenciales errores, impidiendo mantenimientos onerosas y problemas a los aparatos. Incluso, los datos recopilados de estos aparatos pueden utilizarse para mejorar sistemas y mejorar la exposición en sistemas de exploración.
Las zonas de utilización de los equipos de equilibrado abarcan múltiples ramas, desde la fabricación de vehículos de dos ruedas hasta el monitoreo ambiental. No importa si se habla de extensas elaboraciones industriales o modestos establecimientos hogareños, los aparatos de balanceo son necesarios para proteger un desempeño productivo y sin riesgo de interrupciones.